Refurbishing train components plays a pivotal role in extending the operational life of rail vehicles, ensuring passenger safety, and maintaining their aesthetic quality. Over time, these components experience deterioration due to environmental exposure, mechanical stress, and the demands of daily use. Through meticulous and advanced refurbishment processes, operators can restore and even enhance these components to meet or exceed modern engineering and safety standards.
Refurbishing Train Exterior Panels
Exterior panels are the outermost protective layer of trains and trams, shielding them from environmental factors such as rain, wind, debris, and UV exposure. These panels are essential not only for maintaining the vehicle’s aesthetic appeal but also for preserving its structural integrity, ensuring passenger safety, and preventing further damage to internal components. Over time, these panels can become compromised due to weathering, impacts, and general wear and tear, necessitating comprehensive refurbishment to restore their function and appearance.
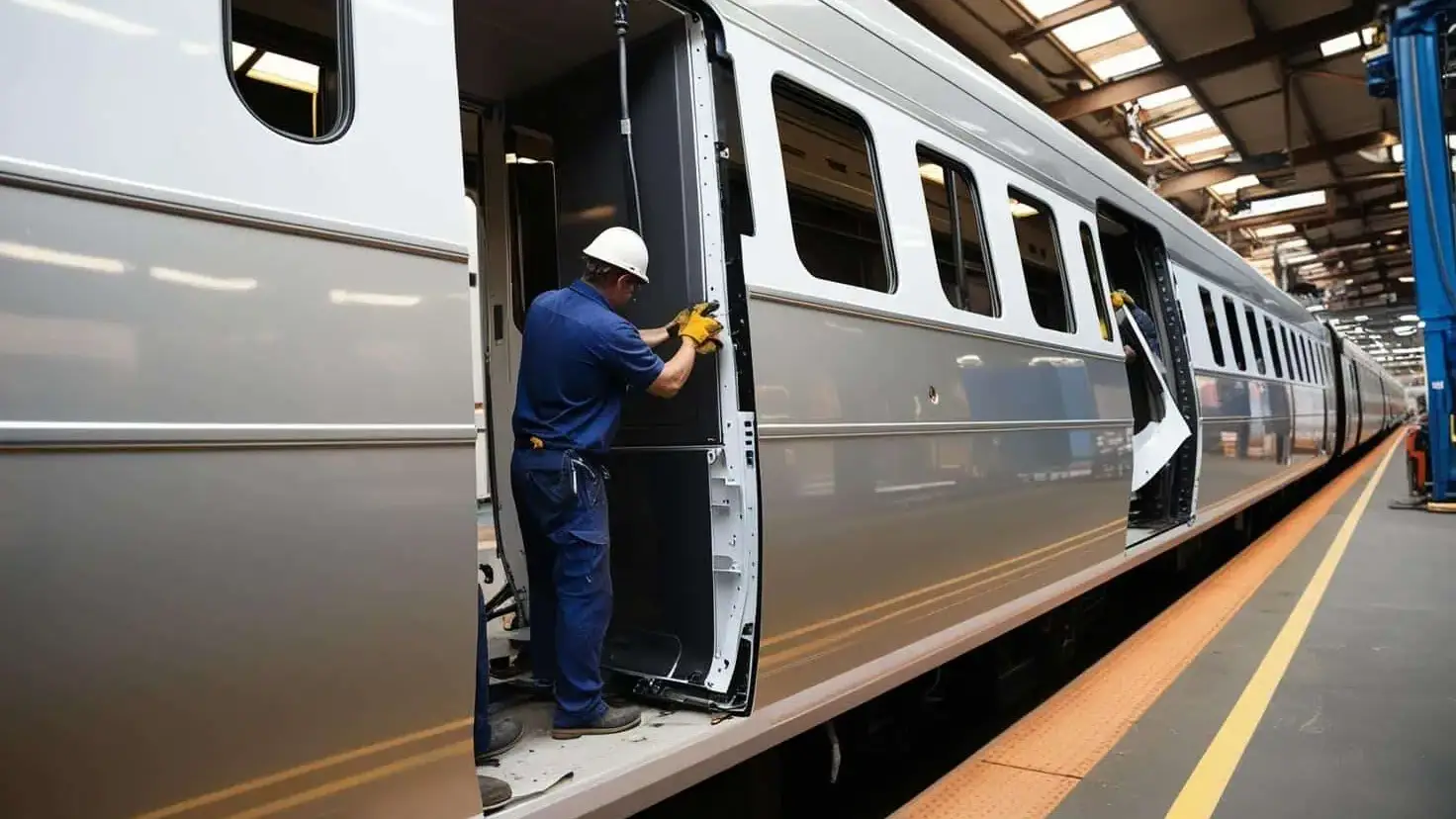
Disassemble
The refurbishment process begins with the careful removal of exterior panels from the vehicle, ensuring safety and precision throughout. Technicians first inspect the panel’s attachment points, such as bolts, rivets, or adhesive mounts, to determine the appropriate tools and techniques for detachment. This step often involves using specialised wrenches, drills, or pry bars to loosen fasteners without causing damage to the panel or underlying structure.
Panels are supported throughout the process to prevent accidental dropping or warping. Proper labeling and documentation of each panel and its mounting location are critical for maintaining organisation and ensuring a seamless, accurate reassembly. Additionally, protective coverings may be applied to surrounding components to avoid scratches or debris contamination during the disassembly process.
Evaluate Any Damage
Once removed, the panels are subjected to an in-depth evaluation to identify any corrosion, dents, cracks, or other structural issues. Over time, exposure to harsh weather conditions, UV radiation, and environmental pollutants causes paint to degrade, chip, or fade, leaving the underlying material vulnerable to corrosion and weakening.
Advanced diagnostic tools, such as ultrasonic scanners, X-ray imaging, and laser measurement systems, are used to detect surface and subsurface defects that might compromise the panel’s functionality.
Match the Original Colour
To maintain aesthetic consistency, the original paint color must be matched with high precision. Utilising spectrophotometers and referencing archived paint codes ensures uniformity across all refurbished panels. This step also considers weathering effects on the original paint to achieve a seamless match.
Sand
All surface imperfections, rust, and layers of old paint are removed through a more advanced and time-efficient laser blasting process at Copamate. This cutting-edge technique uses high-intensity laser beams to vaporise surface contaminants and coatings without damaging the panel’s underlying material.
Laser blasting not only reduces the time it takes to prepare the panels but also ensures unparalleled precision and consistency. The result is a smooth, defect-free surface, perfectly primed for repair and coating.
Fill Dents
High-durability fillers, engineered to withstand environmental and mechanical stresses, are applied to repair dents. After curing, the filler is meticulously sanded to ensure a perfectly smooth and integrated surface, ready for priming and painting.
Prime
Applying a primer serves multiple purposes: it enhances paint adhesion, provides corrosion resistance, and creates a uniform base layer. The primer is carefully selected based on the panel’s material to ensure long-term durability under operational conditions.
Paint
Multiple coats of industrial-grade paint are applied to achieve the desired durability and aesthetic standards. Advanced paint technologies, such as UV-resistant topcoats, are incorporated to protect against fading, chipping, and environmental degradation. Each coat is cured under controlled conditions to maximise adherence and finish quality.
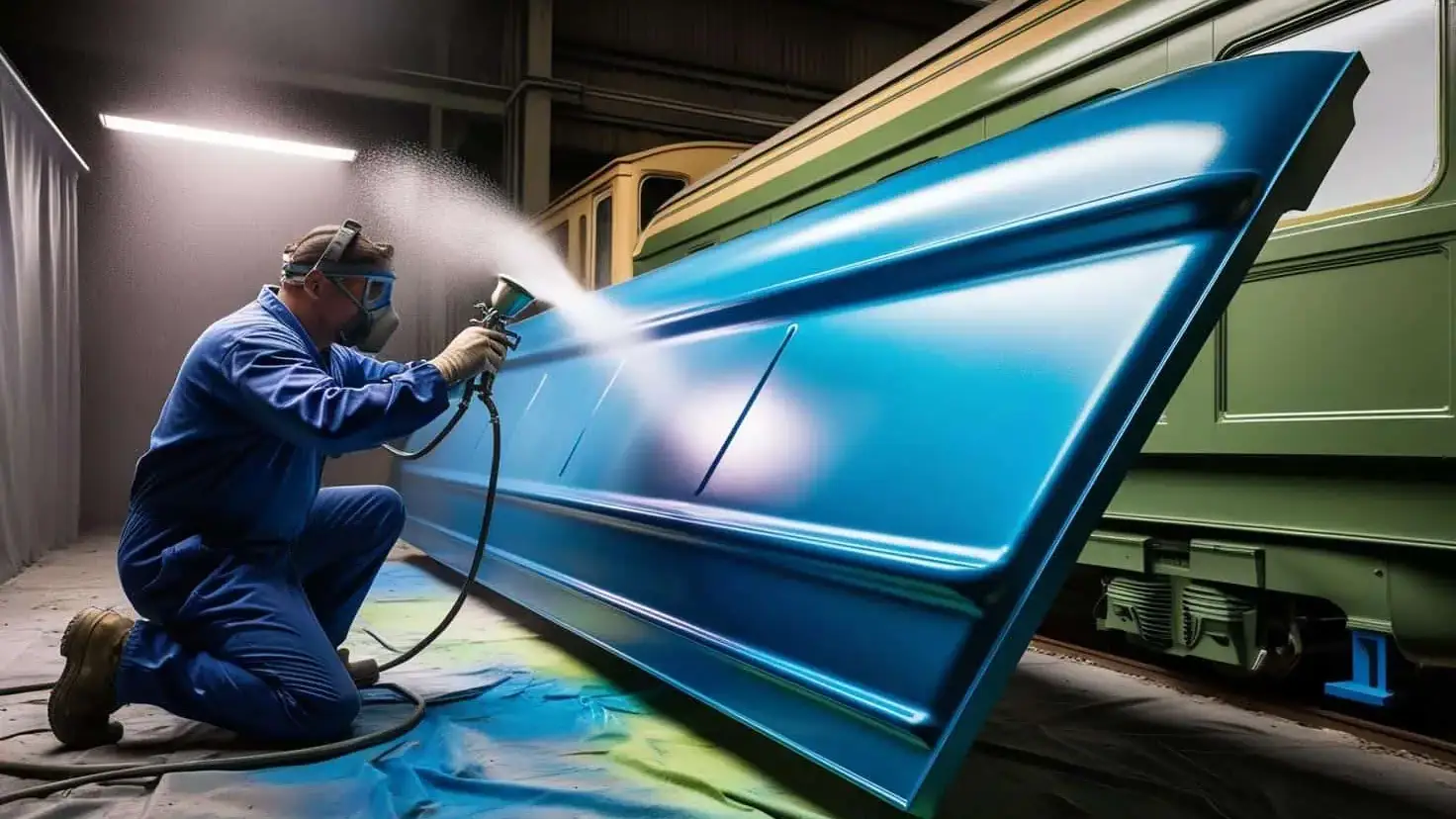
Reassemble
Once the paint has fully cured, the refurbished panels are reinstalled onto the train or tram. During this process, engineers verify the alignment and secure attachment of each panel to maintain structural integrity and safety.
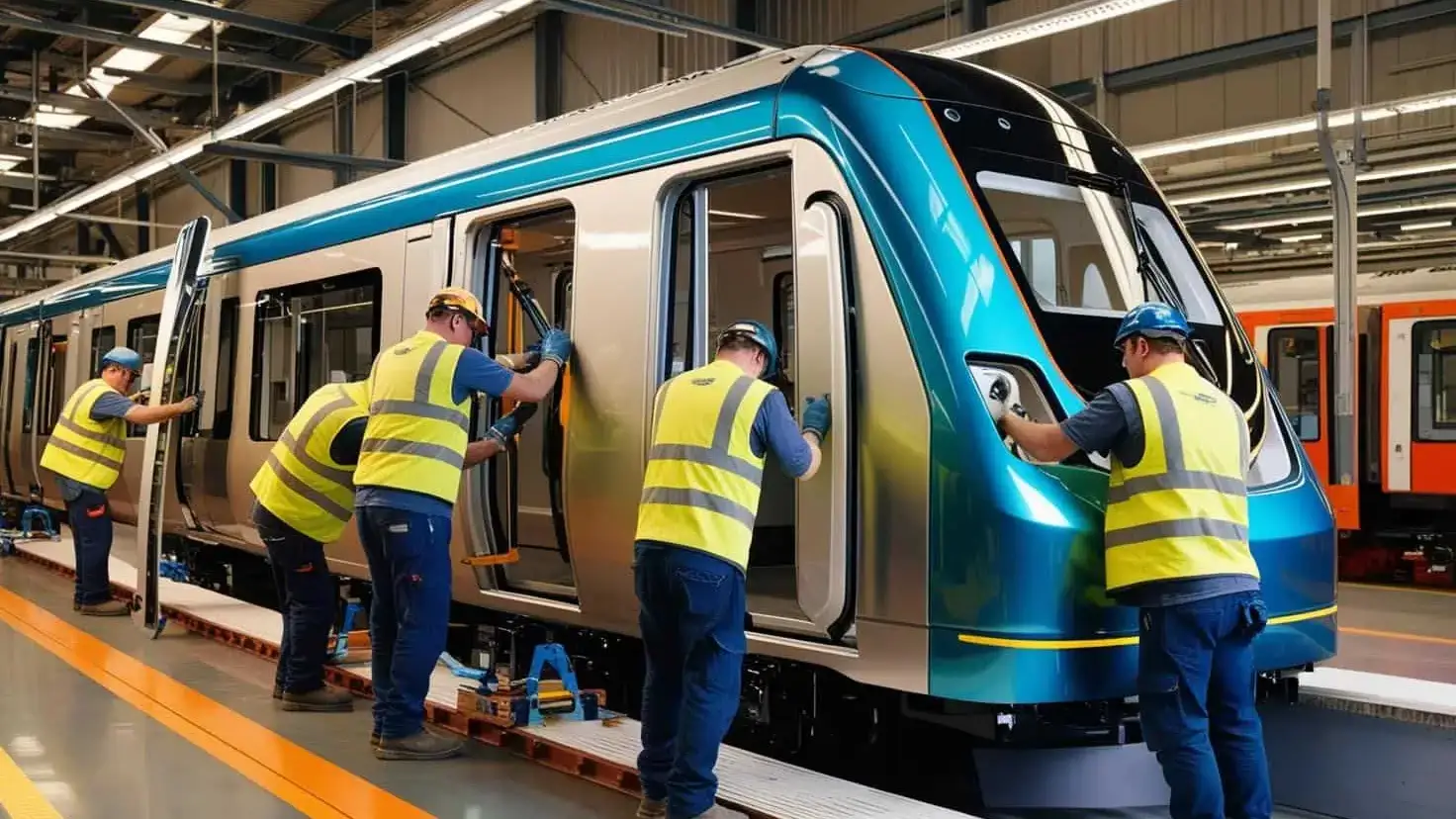
Add Lettering
High-precision digital printing, stenciling, or vinyl application methods are used to add branding, safety information, and other necessary markings. The materials used are designed to withstand environmental exposure while maintaining clarity and durability.
Refurbishment for Train Bogies
Bogies are the cornerstone of a rail vehicle’s performance, bearing its weight, guiding its movement, and ensuring passenger comfort through vibration isolation and suspension systems. Refurbishment of these components is critical for safe and efficient rail operations.
Disassemble
The bogie is removed from the vehicle and disassembled into its core components, including the wheelsets, suspension systems, and the mainframe. This disassembly process ensures that each part can be individually inspected and refurbished.
Cleaning the Train Bogie
Each component undergoes a rigorous cleaning process to remove accumulated dirt, grease, and old lubricants. Industrial degreasers, ultrasonic cleaning systems, and high-pressure washers are employed to achieve a spotless finish, ensuring optimal adhesion for any repairs or coatings.
Apply Cold Spray Additive
Cold spray technology is utilised to restore worn or damaged metal surfaces. This additive manufacturing technique deposits metallic powders at high velocities onto the component without subjecting it to high temperatures, preserving its structural integrity. This method is particularly effective for repairing wheelsets and other high-stress areas.
Testing
Once reassembled, the bogie undergoes extensive testing to validate its functionality and durability. These tests include load-bearing assessments, dynamic performance simulations, and ultrasonic inspections to detect internal flaws. Each test ensures that the bogie meets or exceeds safety and performance standards before reinstallation.
Refurbishment for Train Doors
Train and tram doors are critical for passenger safety and convenience. Refurbishing these components restores their aesthetic appeal and ensures reliable operation in demanding conditions.
Disassemble
The refurbishment process begins with the careful removal of the doors from the vehicle. This step allows for detailed inspection and easier access to internal mechanisms. Accurate documentation is maintained to ensure proper reinstallation.
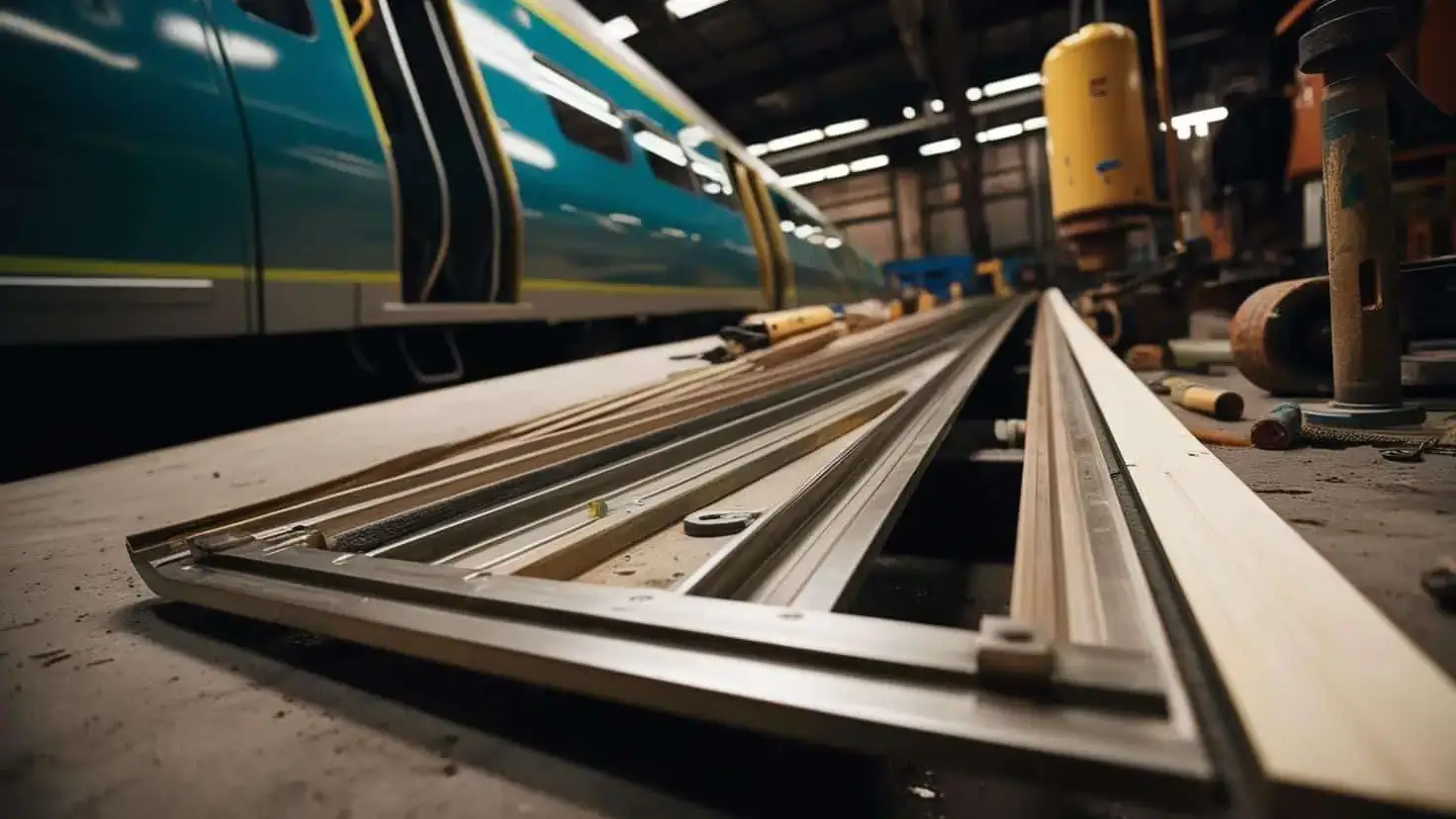
Evaluate Any Damage
A thorough evaluation identifies structural issues, such as dents, cracks, or warping, as well as mechanical problems in hinges, seals, and locking systems. Advanced diagnostic tools may be used to assess the condition of moving parts.
Cleaning The Train Door
All door components are meticulously cleaned to remove accumulated dirt, grease, and any residual paint. Moving parts, such as hinges and sliding mechanisms, are given special attention to ensure smooth operation after reassembly.
Fill Dents
Dents are repaired using high-strength fillers designed for durability under frequent use. After application, the treated areas are sanded to achieve a flawless surface ready for priming and painting.
Prime
The priming process creates a durable base layer that enhances paint adhesion and provides additional protection against corrosion. Specialised primers are selected based on the material composition of the doors.
Paint
Doors are coated with industrial-grade paints formulated for high durability and resistance to environmental factors. Multiple coats are applied, and a protective clear layer may be added to extend the lifespan of the finish.
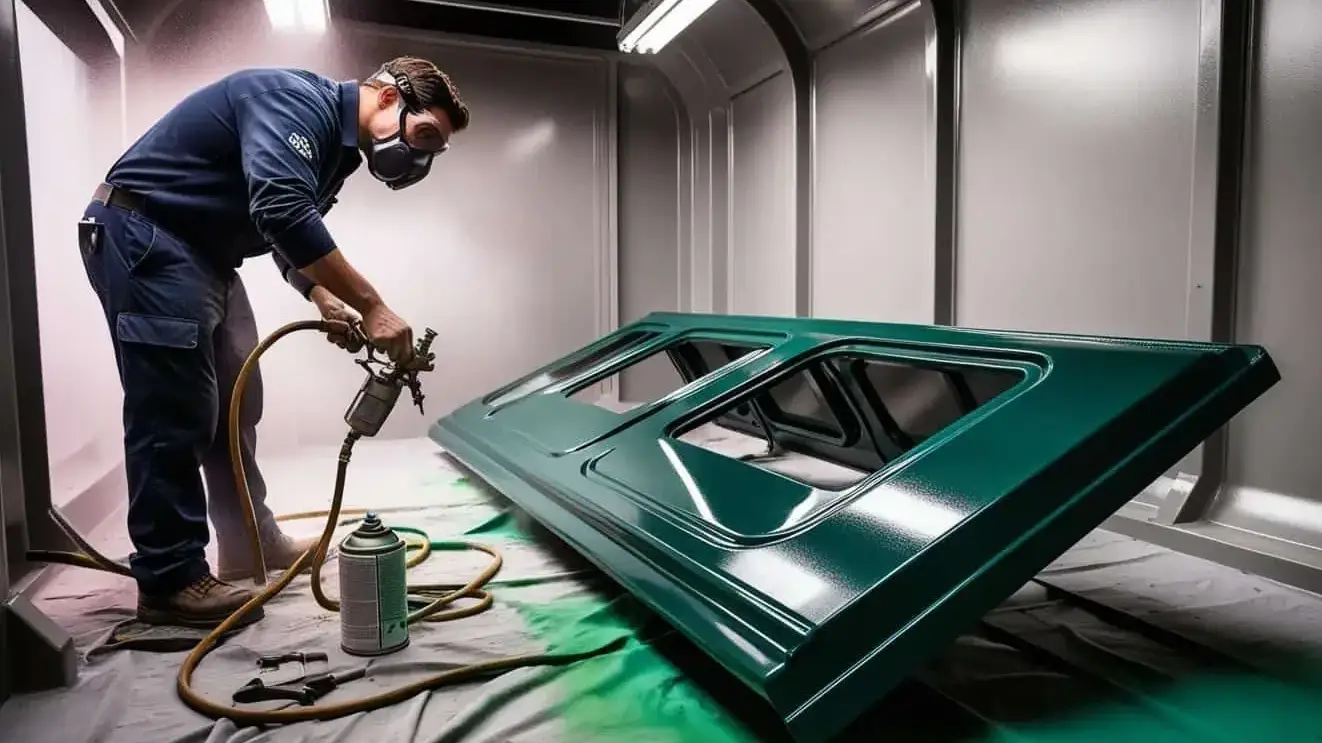
Reassemble
Refurbished doors are reinstalled with careful alignment to ensure proper functionality. Moving parts are lubricated, and adjustments are made to optimise performance and prevent wear over time.
Add Lettering
Safety instructions, operational markings, and branding are applied using high-precision techniques. These markings are designed to remain legible and intact under heavy use and environmental exposure.
Check for Loose Parts
A final inspection ensures that all door components are securely fastened and fully operational. This step guarantees passenger safety and prevents operational disruptions.
Challenges and Outcomes
Refurbishing train and tram components involves addressing numerous technical and logistical challenges. These include strict compliance with safety standards, sourcing high-quality materials, minimising operational downtime, and integrating modern technologies. Despite these challenges, the outcomes of a well-executed refurbishment process are substantial:
- Extended Lifespan: Refurbishment significantly prolongs the service life of critical components, delaying the need for costly replacements.
- Enhanced Aesthetics: Restored exterior and interior components improve the overall appearance of rail vehicles, enhancing the passenger experience.
- Improved Performance: Mechanical repairs and upgrades ensure greater reliability, safety, and efficiency.
- Cost Efficiency: Refurbishment offers a cost-effective alternative to new component manufacturing, optimising resource allocation.
Refurbishing train and tram components is a sophisticated process requiring a combination of advanced technologies, skilled labor, and rigorous quality control. By adhering to meticulous procedures, rail operators can maintain their fleets at peak performance while optimising costs and ensuring the safety and satisfaction of passengers.
Get insights on industry news and posts.
Related Posts
July 24, 2025
Tooling, Fixtures & Jigs Overview | Rail Applications
Tooling, jigs & fixtures is the physical interface between the design and the…
July 3, 2025
Melbourne Metro Tunnel Project | 2025 Update
Melbourne’s Metro Tunnel Project, set to open 2025 is the largest rail…
May 27, 2025
Future Fleet Program Overview | Top 5 Benefits
With the announcement of the Future Fleet Program, New South Wales has…