Precision machining is the process of removing material from a workpiece with extreme accuracy, using computer-controlled tools to produce components with tight tolerances, exact dimensions, and superior surface finishes. This capability is crucial in sectors where even a micron of deviation can mean product failure, such as aerospace, medical, defence, and electronics.
Unlike conventional machining, precision machining is not just about shaping a part, it’s about engineering with certainty. With tolerances often in the range of ±0.0001 inches (2.5 microns) or tighter, this discipline involves an interplay between digital design, high-performance CNC machinery, premium tooling, skilled operators, and rigorous quality control systems.
How Precision Machining Works
At the core of the process is CNC (Computer Numerical Control) technology. Engineers first create a CAD (Computer-Aided Design) model of the component. That model is converted into machine-readable instructions via CAM (Computer-Aided Manufacturing) software. From there, CNC machines, whether mills, lathes, grinders, or EDM machines execute the instructions with robotic precision.
Key Aspects of Precision Machining Include:
- Tool path optimisation to reduce vibration and maximise accuracy
- Thermal stability controls to maintain tolerance consistency
- Multi-axis machining (3, 4, and 5-axis) for complex geometries
- Live tooling and simultaneous operations for efficiency
- CMM (Coordinate Measuring Machines) and metrology tools for inspection
These processes are often supported by automated workflows, digital quality tracking, and Industry 4.0 systems to ensure reproducibility and traceability in high-stakes production environments.
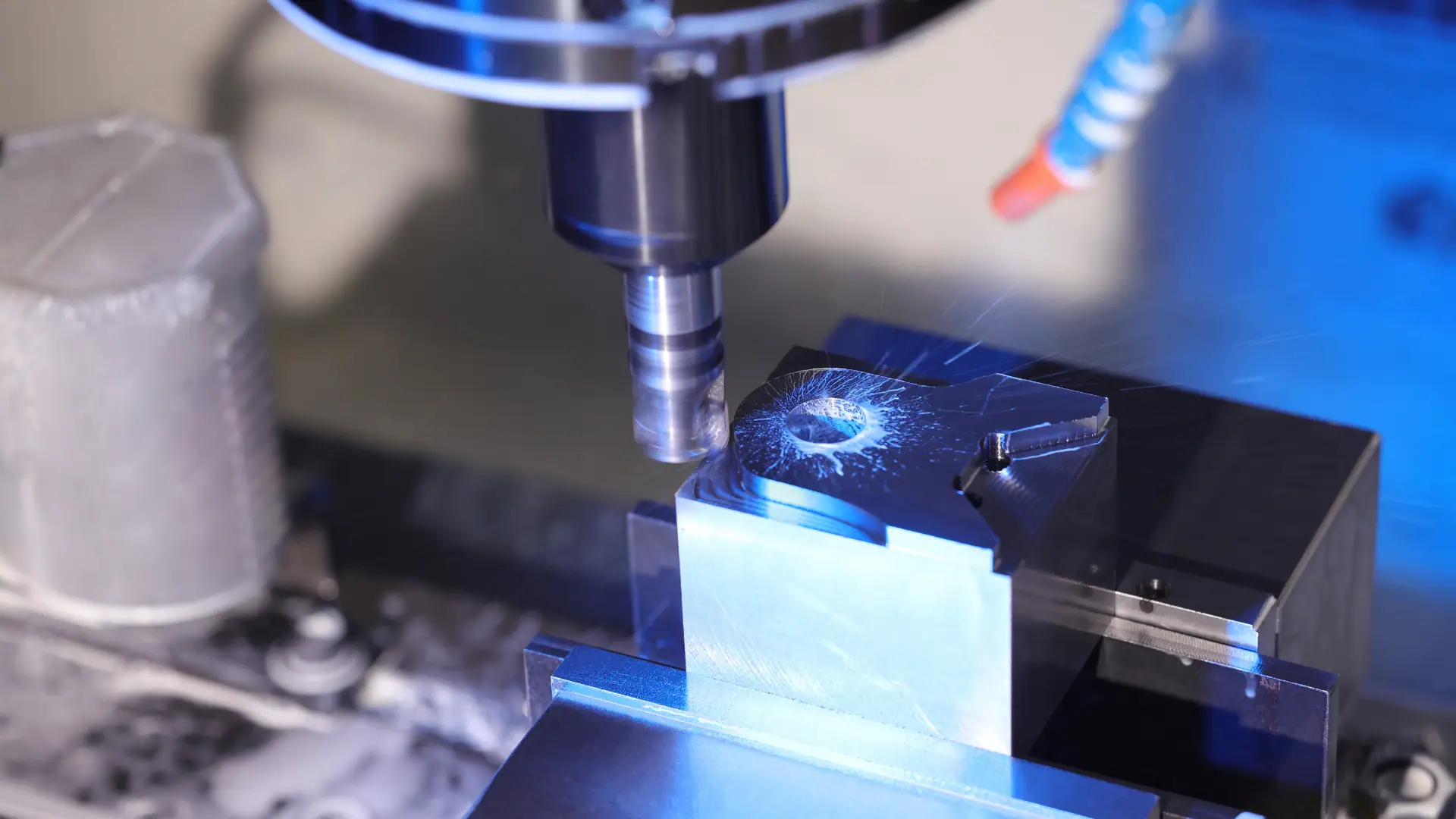
The History and Evolution of Precision Machining
From Manual Craftsmanship to Robotic Accuracy
Precision machining has come a long way since its roots in the Industrial Revolution, where artisans used lathes and milling machines to hand-craft precision parts for steam engines and firearms. The invention of numerical control (NC) in the 1940s and the subsequent rise of CNC in the 1970s marked a turning point, allowing for:
- Automation of complex geometries
- Mass production of high-accuracy parts
- Digital repeatability across factories and global supply chains
Today, modern CNC precision machining blends advanced software, real-time monitoring, high-speed spindles, and AI-assisted quality control, making it the backbone of high-value manufacturing.
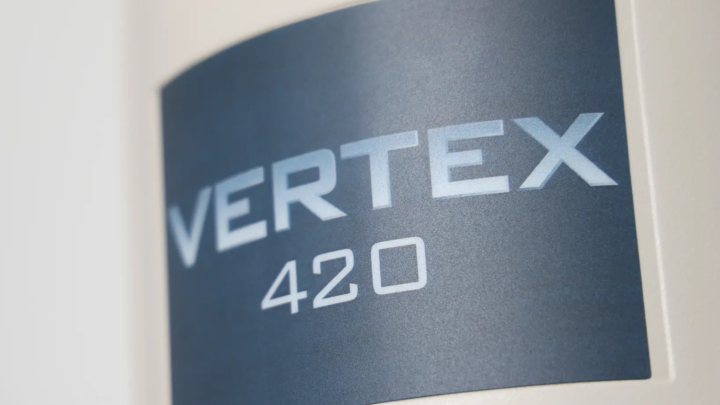
Why Precision Machining is Essential for Aerospace and Tight Tolerance Applications
Safety, Compliance, and Performance
Aerospace is arguably the most demanding industry when it comes to precision, reliability, and traceability. A single aircraft contains millions of individual components, each of which must meet stringent aerospace material and dimensional standards, such as AS9100 and NADCAP.
Even minor discrepancies in part dimensions can lead to:
- Stress fractures in high-load components
- Vibration-induced fatigue in engine parts
- System incompatibility during assembly
- Catastrophic failure during operation
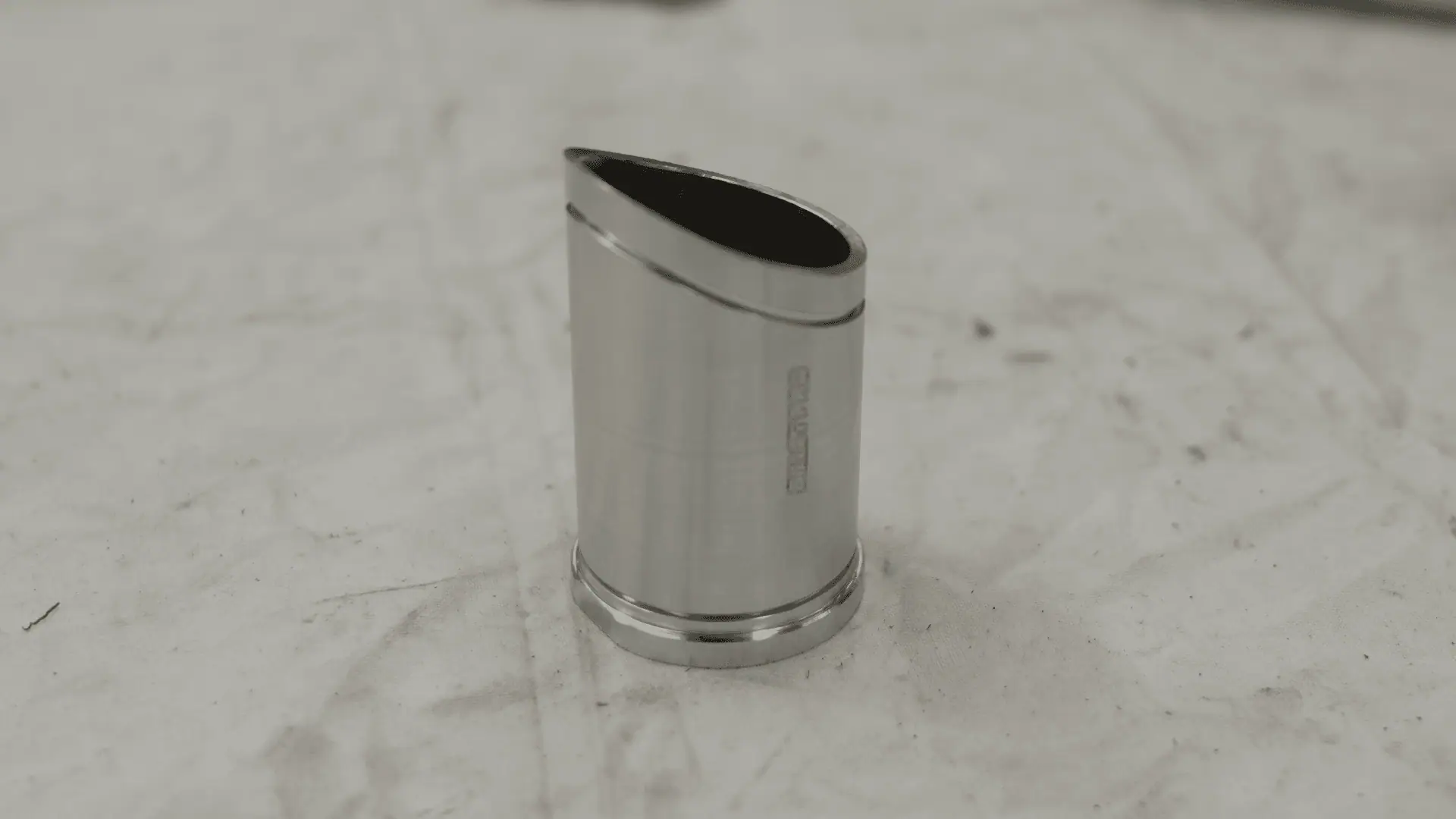
Mission-Critical Components That Rely on Precision
- Turbine blades: Require balanced mass distribution and perfect aerodynamic geometry
- Landing gear components: Must endure repeated stress cycles without deformation
- Fuel system parts: Require ultra-tight seals to prevent leaks under high pressure
- Avionics enclosures: Must shield sensitive electronics from heat and EMI
Material Challenges in Aerospace Precision Machining
Machining aerospace parts isn’t just about tight tolerances, it’s also about handling advanced, exotic materials such as:
- Titanium alloys: Lightweight and strong, but difficult to cut
- Inconel and Hastelloy: Heat-resistant superalloys
- Carbon fibre-reinforced composites: Delicate to machine without delamination
- Aluminium 7075 and 6061: Require precision balancing strength and weight
Each material presents its own thermal expansion, chip control, and tool wear challenges, all of which must be accounted for in the machining process.
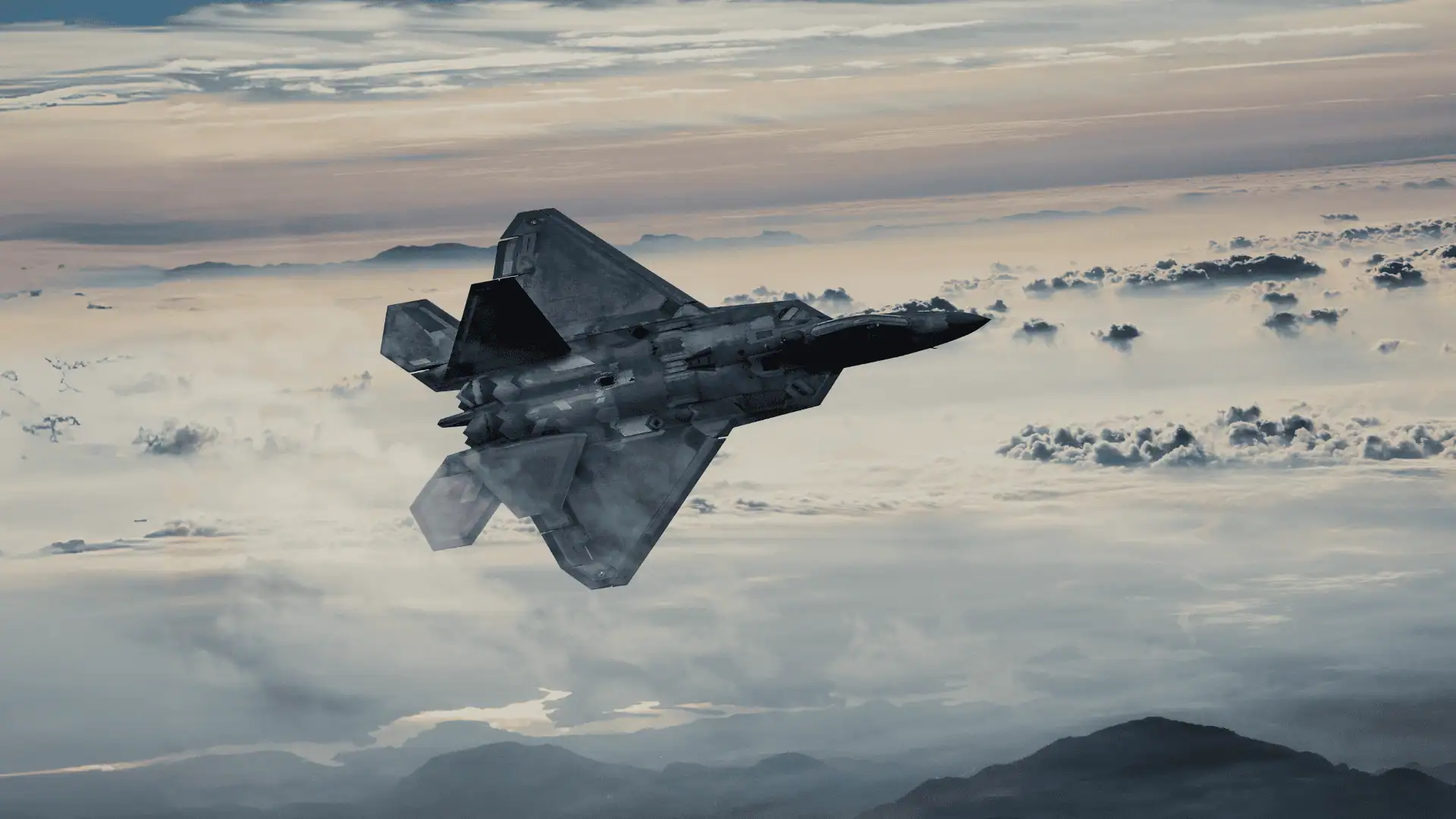
CNC Milling vs CNC Turning in Precision Machining
While both are subtractive manufacturing processes, CNC milling and CNC turning serve different roles and require different setups, tooling, and skillsets.
CNC Milling – Complex Geometries, Multi Axis Movement
Milling involves a rotating cutting tool that moves across a stationary workpiece. Multi-axis CNC mills can produce complex 3D shapes, making them ideal for parts with:
- Pockets, slots, contours
- Intricate surface finishes
- Threaded holes and tapped features
- Undercuts and dynamic angles (via 4- or 5-axis machines)
Modern 5-axis milling enables operations from multiple directions in a single setup, critical for both speed and accuracy.
CNC Turning – Precision in Symmetry
Turning uses a rotating workpiece and fixed cutting tools. It’s the go-to choice for cylindrical components that require:
- High-speed production
- Uniform roundness
- Smooth surface finishes
- Fine tolerances on diameters and bores
Turned parts include shafts, pins, valve stems, spacers, and bushings, many of which are central to fluid control, motion transfer, and load-bearing applications.
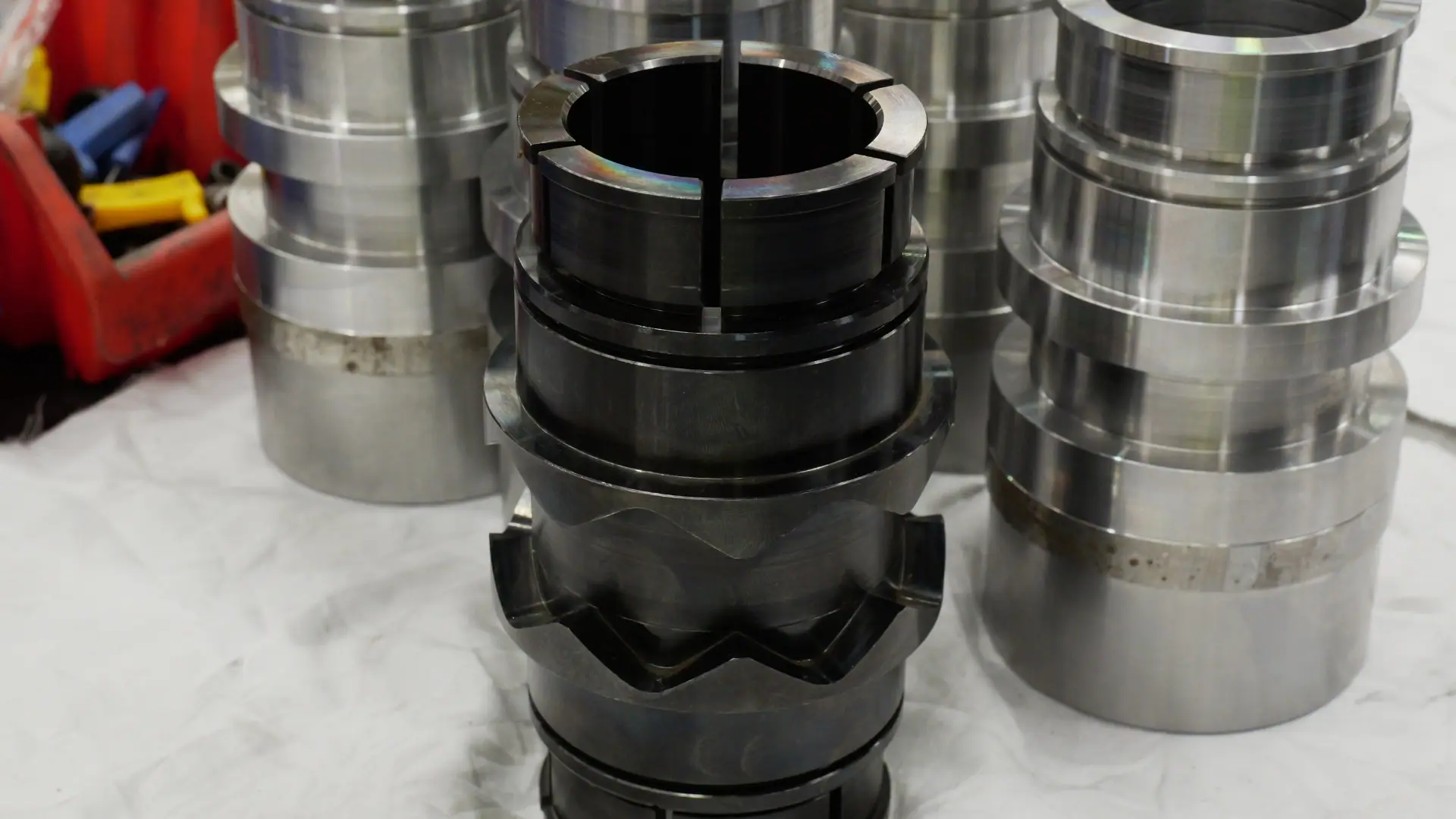
Summary of Differences Between Milling and Turning
Feature | CNC Milling | CNC Turning |
Machine movement | Rotating tool, stationary part | Rotating part, stationary tool |
Ideal part shapes | Prismatic, complex 3D | Cylindrical, rotationally symmetric |
Axis support | 3 to 5-axis | Typically 2 to 4-axis |
Material removal speed | Moderate | Very high for round stock |
Typical tolerance range | ±0.0002” or better | ±0.0001” or better |
Common applications | Brackets, housings, 3D contours | Shafts, pistons, rollers, bushings |
Industries That Depend on Precision Machining
Aerospace & Defence
As previously discussed, aerospace components live under extreme physical and regulatory pressures. Defence parts often go further, requiring additional security protocols and certifications for parts that are:
- Used in military-grade aircraft
- Built into radar and targeting systems
- Embedded into missile guidance or naval propulsion systems
Suppliers must meet defence contracting rules, such as DISP, ITAR, DFARS compliance, and cybersecurity standards, making the machining requirements as much about data integrity as physical precision.
Medical & Biomedical
In medical device manufacturing, parts not only need to be accurate, they must be safe for human implantation or contact. Precision machining supports:
- Titanium bone plates and screws
- Orthopaedic joint replacements
- Surgical instruments with micro-tips
- MRI-compatible equipment (non-magnetic materials)
Electronics & Photonics
The electronics industry demands precision in microns, particularly for high-frequency and high-speed devices. Common applications include:
- Housings for optical sensors
- Heat sinks with tight tolerances for thermal performance
- RF shielding enclosures
- Circuit board supports
Automotive & Motorsports
From gearboxes to custom throttle bodies, precision machining enables performance tuning and innovation in the automotive and motorsport world. Race teams, in particular, rely on machined parts that maximise power-to-weight ratios without compromising durability.
Renewable Energy & Power Generation
Whether it’s a hydroelectric turbine, solar tracking system, or nuclear control rod, energy infrastructure relies on tight-fitting, corrosion-resistant components that can last decades under stress.
Advantages of Precision Machining
1. Unmatched Accuracy
Precision machining allows manufacturers to maintain incredibly tight tolerances with consistency across thousands of units, a non-negotiable for industries that demand perfect parts every time.
2. Material Versatility
Modern CNC machines can handle a wide range of materials, including:
- Stainless steel
- Titanium
- Aluminium
- Engineering plastics
- Brass, copper, bronze
- Hardened tool steels
3. Reduced Waste, Increased Efficiency
Because the cutting path is programmed and optimised digitally, material is removed only where needed, reducing waste and improving overall yield — a win for both economics and sustainability.
4. Compatibility with Automation and Metrology
Precision machining integrates with robotics, inspection systems, and automated feedback loops, making it compatible with lights-out manufacturing and smart factory environments.
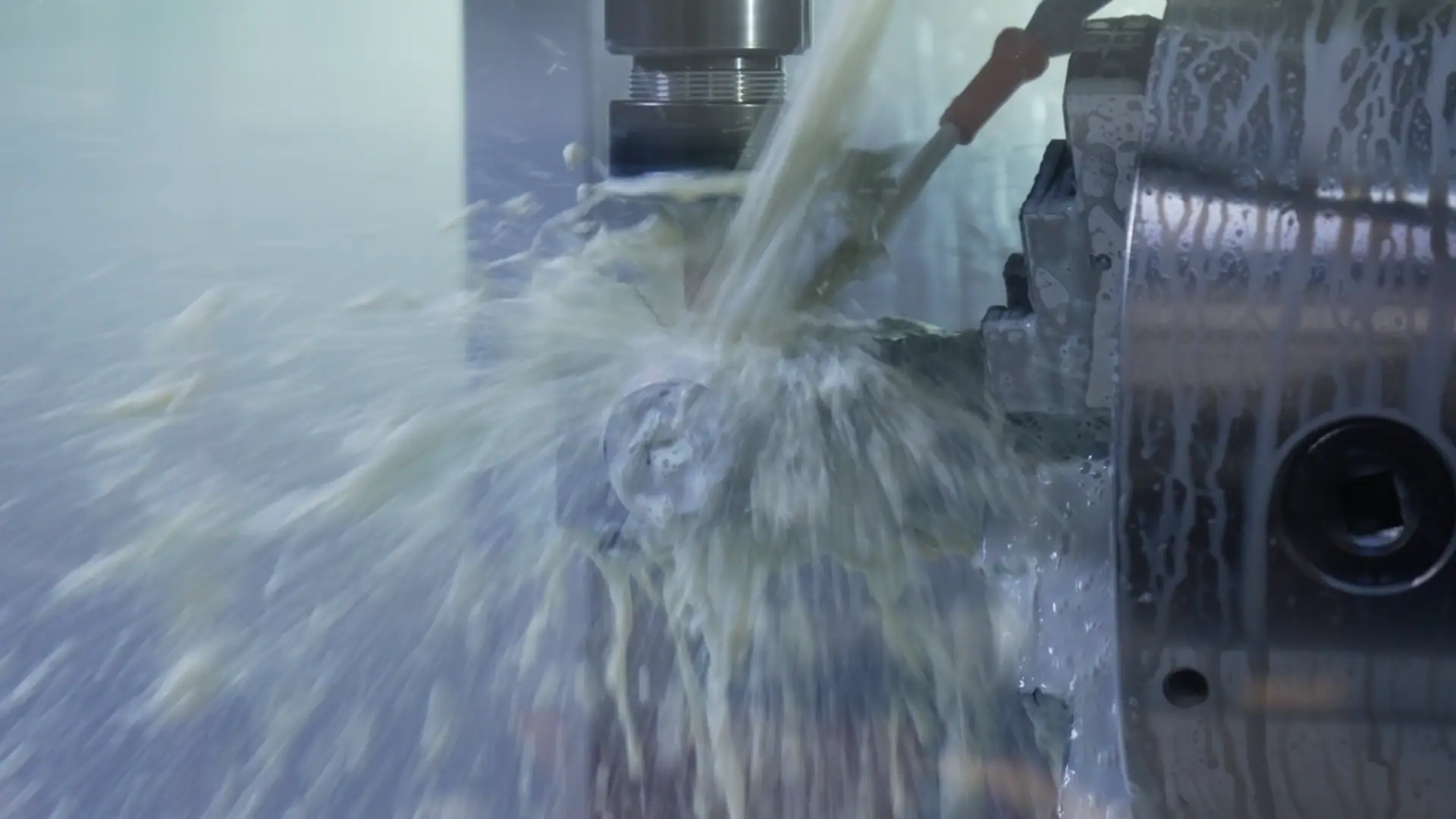
The Future of Precision Machining
1. AI-Enhanced Tool Path Optimisation
Artificial Intelligence and Machine Learning are beginning to automate decision-making in tool selection, cut strategy, and predictive maintenance, unlocking new levels of autonomy and efficiency.
2. Hybrid Manufacturing (Additive + Subtractive)
Combining 3D printing and CNC machining is creating new opportunities for net-shape manufacturing, particularly in aerospace where lightweight internal geometries must meet precise external mating features.
3. Ultra-Miniature and Nano-Machining
As industries like photonics and quantum computing advance, demand for nano-scale components will grow — pushing precision machining into entirely new technical domains.
Final Thoughts – Precision Machining as the Backbone of Innovation
Precision machining is far more than a manufacturing method — it’s an enabler of innovation, safety, and performance. It bridges the gap between design and functionality, giving engineers the confidence to push boundaries and industries the tools to build what was once impossible
.
In a world increasingly defined by technological integration, miniaturisation, and performance under pressure, precision machining will remain one of the most critical processes in modern manufacturing.
Whether it’s launching spacecraft, performing life-saving surgeries, or delivering energy to millions, precision machining is the silent force that makes it all work to the micron.
Get insights on industry news and posts.
Related Posts
July 24, 2025
Tooling, Fixtures & Jigs Overview | Rail Applications
Tooling, jigs & fixtures is the physical interface between the design and the…
April 29, 2025
Types of CNC Machines & Their Role in Aerospace, Automotive & Rail
The types of CNC Machines can vary from the number of axes on a CNC machine has…
November 29, 2024
CNC Machine Maintenance | Expert Guide
CNC machine maintenance is required for proper care to continue performing at…