Metal fabrication is an important component of modern industrial businesses, and the global market is expected to increase at a compounding annual growth rate of 3.5% from 2021 to a startling $23.8 billion by 2030. Fabricated metal is the foundation of modern infrastructure, from bridges and skyscrapers to common automobiles. It maintains transportation systems, promotes manufacturing, and fosters technological innovation. What is metal fabrication exactly? This comprehensive post examines the complex field of metal fabrication, examining its commercial, structural, and industrial uses as well as the procedures and standards that ensure its quality.
What is Metal Fabrication?
Metal fabrication is the intricate process of forming, cutting, and assembling metal into useful structures or products. It combines cutting-edge technology, engineering accuracy, and workmanship to turn raw metal materials into customised parts. Processes such as forming, fusion welding, and machining are used to meet project specifications. Copper, aluminum, and steel are common materials that are chosen for their special qualities to guarantee that each application serves its intended function.
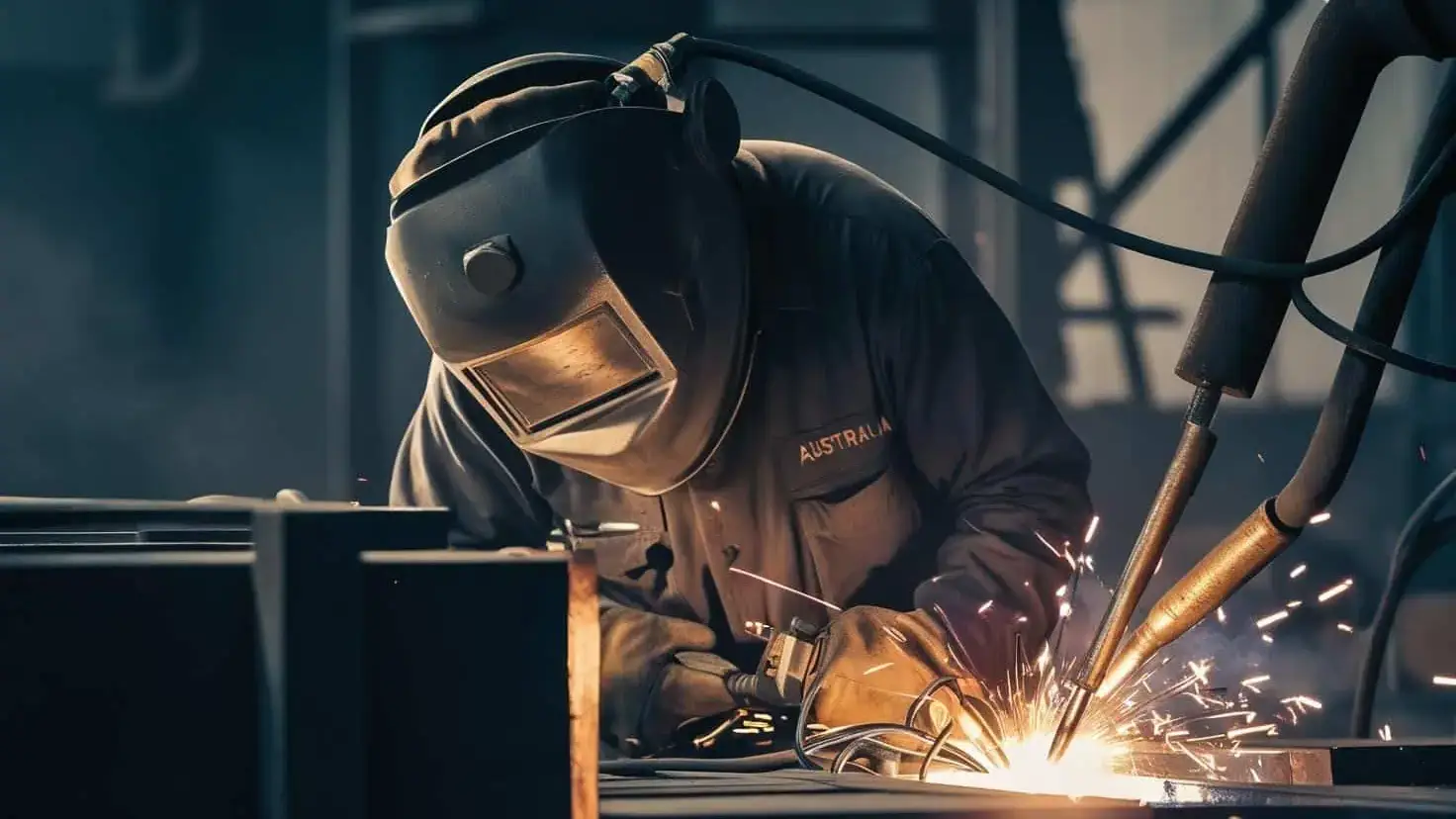
For the production of necessary equipment, parts, and structures, industries like manufacturing, automotive, aerospace, and construction mostly rely on metal fabrication. Metal fabrication demonstrates versatility by producing intricate parts for big machinery or unique railings for structures. From tiny brackets to complex machinery, its uses highlight how essential it is to the development of infrastructure and technology.
What is Industrial Metal Fabrication?
Industrial metal fabrication involves the creation of robust parts and equipment specifically designed to endure the demanding conditions of industries like oil and gas, mining, and large-scale manufacturing. This category is distinguished by its scale, complexity, and emphasis on durability. Key characteristics of industrial fabrication include:
- Large-Scale Machinery and Specialised Tools: Employed to manage intricate and robust projects.
- High-Strength Materials: Structural steel and advanced alloys are commonly used to ensure longevity and resilience.
- Sophisticated Techniques: Technologies such as plasma cutting, CNC machining, and heavy-duty welding are staples.
Industrial fabrication prioritises precision and durability, ensuring components perform consistently under extreme conditions. Typical outputs include oil pipelines, industrial machinery frames, and heavy-duty brackets. These components form the backbone of infrastructure and large-scale industrial operations, enabling technological progress and economic reliability.
What is Structural Metal Fabrication?
The primary goal of structural metal fabrication is to create essential parts for infrastructure and structures. It is distinguished by outstanding strength, stability, and strict safety regulations. Typical goods consist of:
- Beams, Columns, and Trusses: Forming the core framework of buildings, bridges, and other structures.
- Staircases, Handrails, and Mezzanines: Adding functionality and accessibility to architectural designs.
- Frameworks for Towers and Infrastructure: Supporting large-scale projects like transmission towers and expansive bridges.
Components made using this process are guaranteed to meet strict quality and safety standards. Structural steel components in Australia are governed by the AS/NZS 5131:2016 Structural Steelwork – Fabrication and Erection standard, which guarantees its dependability and durability. Structural fabrication is essential to modern engineering and architecture, from bridges to skyscrapers.
What is Commercial Metal Fabrication?
Commercial metal fabrication serves companies that need unique metal items that combine practicality and style. Special needs in public, office, and retail settings are met by this kind of fabrication. Typical instances include of:
- Display Racks and Shelving: Optimised for retail environments while enhancing visual appeal.
- Custom Signage and Architectural Features: Designed to reflect branding and capture attention.
- Office Furniture: Combining durability and design for desks, partitions, and storage solutions.
Commercial fabrication often incorporates intricate designs and finishes, ensuring alignment with a business’s branding and operational goals. From sleek office interiors to visually striking retail displays, commercial metal fabrication helps businesses make an impactful impression.
What is The Metal Fabrication Process?
The metal fabrication process is a meticulously planned sequence that transforms raw materials into refined products. This process typically involves three main phases:
1. Design and Engineering:
-
- CAD (Computer-Aided Design) software generates precise blueprints detailing every project element.
- Engineers ensure the designs meet aesthetic, functional, and structural requirements.
2. Material Preparation:
-
- Raw metal is cut, shaped, or treated to align with design specifications.
- Advanced tools, such as laser cutters or press brakes, prepare components for assembly.
3. Assembly and Finishing:
- Components are welded, bolted, or otherwise joined to create the final structure.
- Finishing processes like powder coating, painting, or polishing enhance durability and aesthetics.
This structured approach guarantees that the final product meets high standards of functionality, precision, and visual appeal.
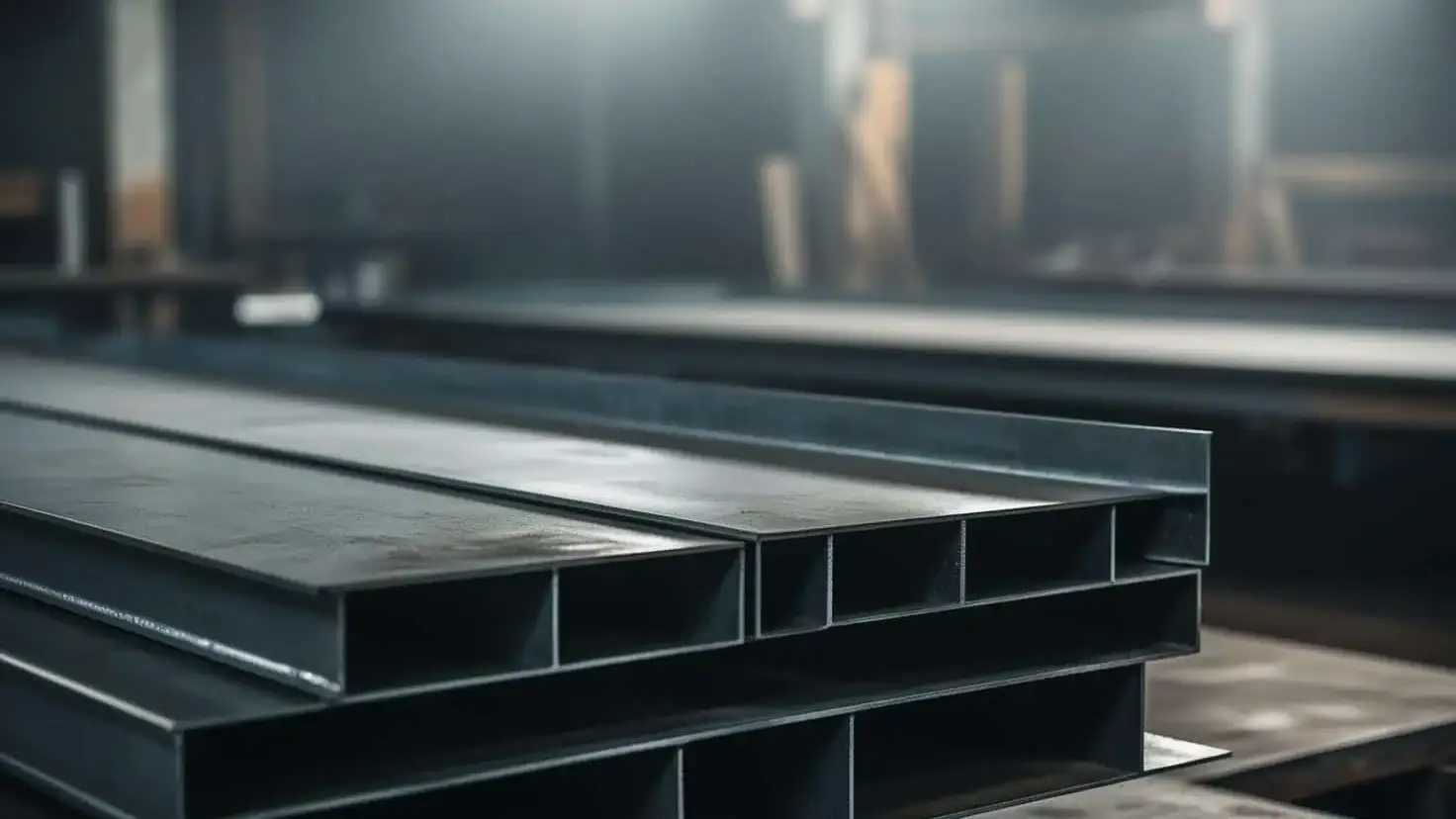
What Are the Main Processes in Metal Fabrication?
Metal fabrication employs an array of specialised processes to achieve precise results. Key processes include:
- Cutting: Techniques like laser cutting, plasma cutting, and water jet cutting ensure accuracy and efficiency.
- Welding: Joining metal components using heat and filler materials to create strong, durable bonds.
- Forming: Metal is bent or shaped using press brakes, rollers, or stamping machines.
- Machining: Precision material removal is achieved using tools like lathes, mills, and drills.
- Finishing: Processes like polishing, anodising, or applying protective coatings enhance durability and aesthetics.
Each step contributes to the overall quality and functionality of the finished product, ensuring it meets project requirements.
Raw Materials
Metal fabrication relies on a variety of raw materials, each chosen for its distinct properties and suitability for specific applications. Commonly used materials include:
- Steel: Valued for its strength and versatility, steel is widely used in structural and industrial applications.
- Aluminum: Lightweight and corrosion-resistant, aluminum is essential in aerospace and automotive industries.
- Copper: Renowned for its conductivity, copper is integral to electrical and thermal applications.
- Stainless Steel: Resistant to corrosion, stainless steel is preferred in architectural, medical, and food industries.
Selecting the appropriate raw material ensures the final product meets both functional and aesthetic requirements.
Is Metal Fabrication Welding?
Although welding is an essential part of metal fabrication, it is simply one facet of the larger field. Using heat and filler material, welding joins two or more pieces of metal. In contrast, metal fabrication is a comprehensive process that includes a wide range of operations, such as cutting, shaping, machining, and assembling.
Metal Fabrication vs Welding
Aspect | Metal Fabrication | Welding |
Scope | Broad (cutting, forming, assembling) | Specific (joining metal parts) |
Processes | Includes welding, machining, etc. | Limited to joining techniques |
Applications | Custom parts, large structures | Repairs, assembly tasks |
Metal Fabrication vs Machining
Aspect | Metal Fabrication | Machining |
Scope | Broad (cutting, forming, assembling) | Precision material removal |
Techniques | Includes welding, forming, etc. | CNC milling, turning, drilling |
Output | Functional components | High-precision parts |
How to Fabricate Metal?
Fabricating metal involves a systematic and rigorous process to ensure precision and quality. Key steps include:
1. Select Materials:
- Choose metals based on project requirements, considering strength, weight, and corrosion resistance.
2. Design the Blueprint:
-
- Develop detailed plans using CAD software to define dimensions and specifications.
3. Prepare the Material:
-
- Use advanced tools like laser cutters and press brakes to cut and shape the material.
4. Assemble the Components:
-
- Join pieces through welding, bolting, or riveting to create the final product.
5. Apply Finishing Touches:
- Enhance durability and aesthetics with coatings, paint, or polish.
These steps ensure the creation of high-quality, reliable components that meet stringent industry standards.
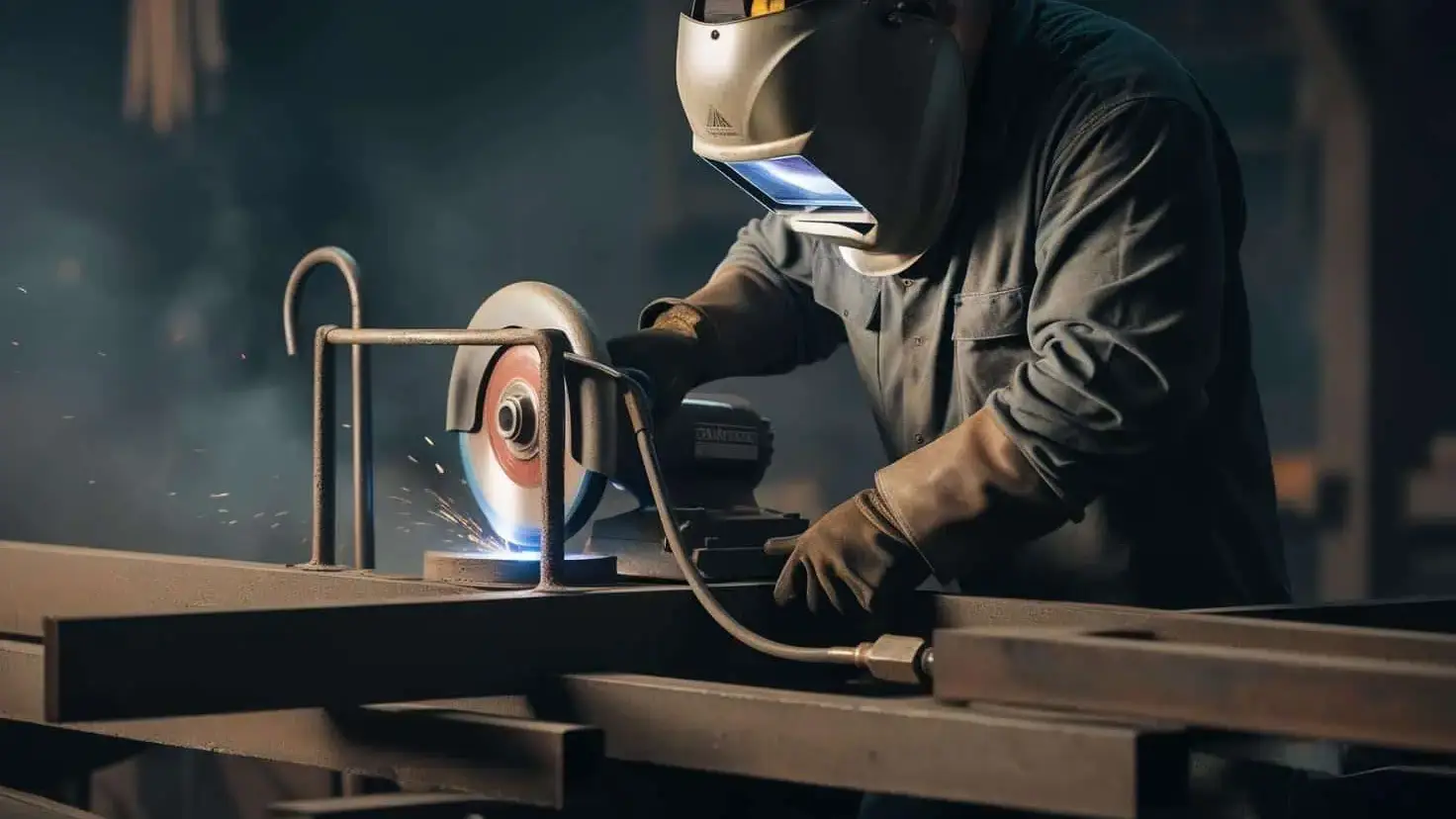
Australian Standard for Structural Steel Fabrication
In Australia, strict quality standards for structural steel fabrication are set under the AS/NZS 5131:2016 Structural Steelwork – Fabrication and Erection standard. The dependability of crucial infrastructure and architectural projects is ensured by adherence to these standards, which guarantee that components fulfill performance, durability, and safety criteria.
Final Notes
Understanding the complexities of metal fabrication enables you to make wise decisions and use this crucial process to accomplish project excellence, regardless of your role as an engineer, project manager, or business owner. Metal fabrication continues to be a key factor in determining the direction of industries around the world due to its enormous potential and unwavering significance.
Get insights on industry news and posts.
Related Posts
July 3, 2025
Melbourne Metro Tunnel Project | 2025 Update
Melbourne’s Metro Tunnel Project, set to open 2025 is the largest rail…
June 27, 2025
Laser Cutting Materials
At Copamate, we specialise in precision laser cutting across a diverse range of…
May 27, 2025
Future Fleet Program Overview | Top 5 Benefits
With the announcement of the Future Fleet Program, New South Wales has…