Computer Numerical Control (CNC) machines have revolutionised manufacturing by offering unparalleled precision and automation. CNC machining is essential for producing highly intricate components across a variety of industries, including aerospace, automotive, and rail. CNC systems operate based on pre-programmed sequences of control commands that guide automated machining processes. Whether it’s a simple lathe or a sophisticated multi-axis CNC machine, the precision and consistency offered by CNC technology are indispensable in producing high-quality components.
As industries continue to evolve, the need for even more precise tolerances, a wider range of materials, and faster production times has driven the ongoing advancement of CNC machinery. This guide explores the different types of CNC machines, how they’re applied in real-world manufacturing, and why they’re essential in industries like aerospace, automotive, and rail.
The Importance of CNC in Aerospace, Automotive, and Rail
Precision machining is critical in sectors like aerospace, automotive, and rail, where even the slightest deviations can have serious consequences. In aerospace, the tolerances can be as tight as ±0.0001 inches, meaning that a single misstep in manufacturing could compromise safety. Similarly, the automotive industry requires the mass production of parts that are identical in every way to ensure reliability, while the rail industry depends on CNC technology for producing durable components with consistent performance.
Aerospace Industry
- Tolerances: ±0.0001 to ±0.0005 inches
- Materials: Titanium, aluminum, Inconel, composites
- Typical Components: Engine mounts, turbine blades, housings, brackets, seat structures
Automotive Industry
- Tolerances: ±0.001 to ±0.005 inches
- Materials: Steel, aluminum, polymers
- Typical Components: Engine parts, camshafts, brake systems, suspension components
Rail Industry
- Tolerances: ±0.005 to ±0.010 inches
- Materials: Cast iron, mild steel, alloys
- Typical Components: Wheel sets, axle boxes, brake discs, structural elements
The need for exacting standards in each of these industries further underscores the importance of CNC machines, which provide repeatable, high-precision results that are essential for manufacturing safe and reliable components.
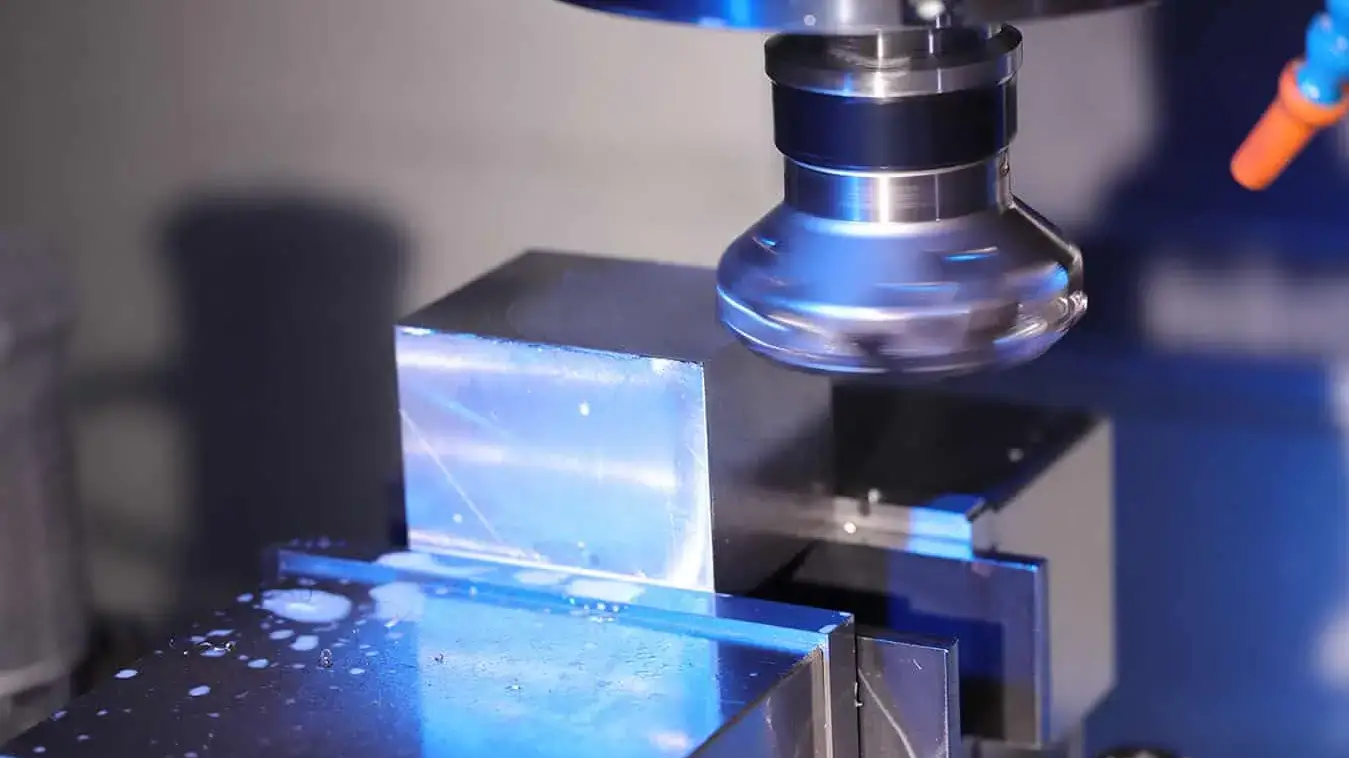
Types of CNC Machines by Axis Complexity
2-Axis CNC Machines (Lathes)
2-axis CNC machines typically operate on the X (horizontal) and Z (vertical) axes, making them ideal for turning cylindrical parts. In these systems, the workpiece is rotated while the cutting tool moves along these two axes, primarily used for basic operations like drilling, threading, and boring.
Applications:
- Cylindrical parts (e.g., shafts, pins)
- Threading and boring operations
- Simple drilling for symmetrical parts
Industries:
- Automotive: Axles, bushings
- Rail: Simple shafts, pins
Tolerances:
- ±0.005″ to ±0.010″
Diameter Ranges:
- 5 mm to 300 mm
Limitations:
- Lacks the ability to perform side or angled machining.
- Best suited for simpler, symmetrical parts.

3-Axis CNC Machines
3-axis CNC machines add a vertical Z-axis to the 2-axis system, enabling milling, drilling, and contouring of more complex shapes. These machines can perform more intricate operations on different surfaces.
Applications:
- Milling slots, holes, and cavities
- 3D contours in dies and molds
Industries:
- Automotive: Gearboxes, cylinder heads
- Aerospace: Housing units, structural parts
- Rail: Brake calipers, suspension parts
Tolerances:
- ±0.001″ to ±0.005″
Part Sizes:
- Up to 1000 mm in length
Advantages:
- Greater flexibility for complex surfaces and 3D machining.
- Suitable for a wide range of components across multiple industries.
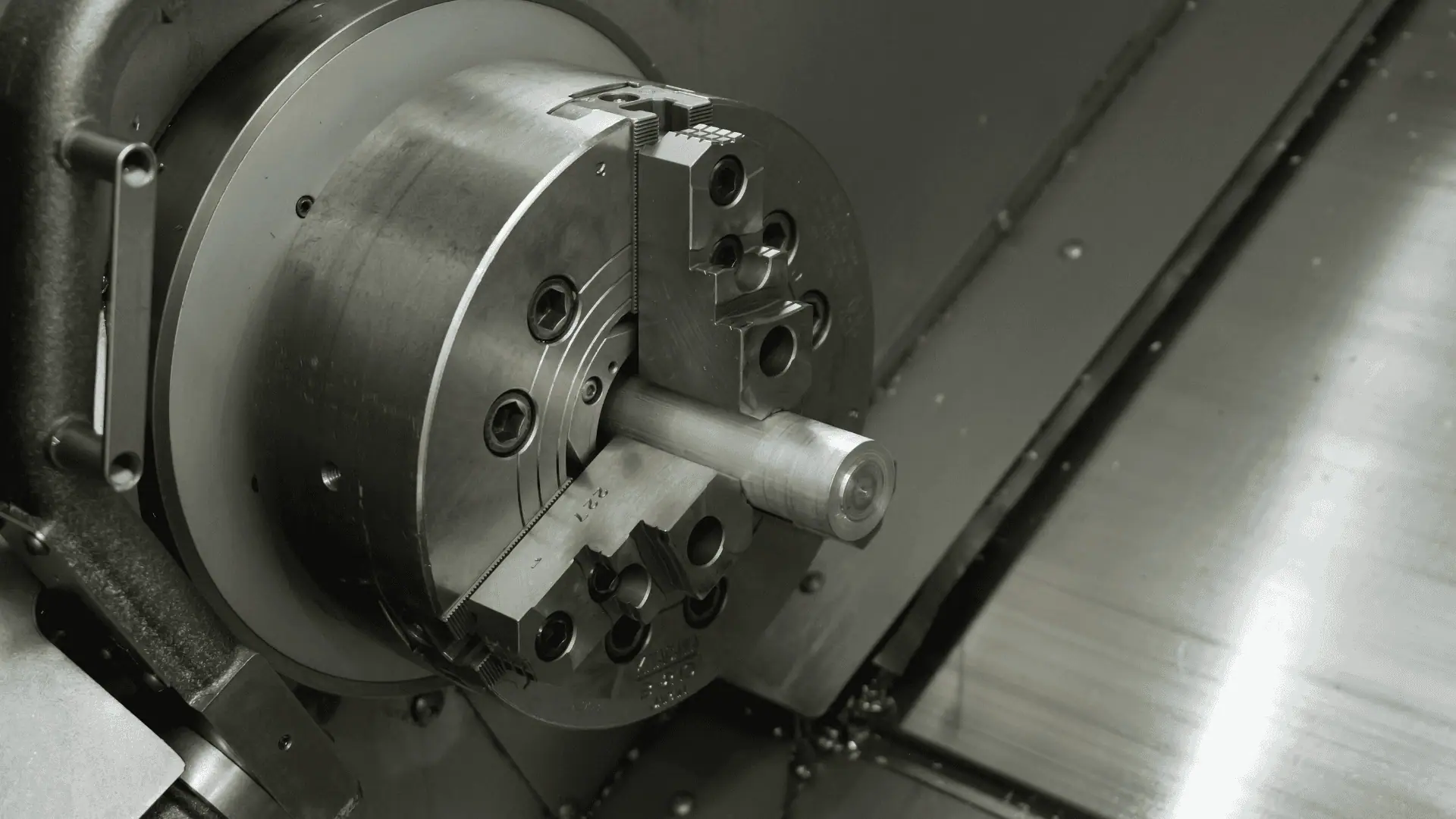
4-Axis CNC Machines
4-axis cnc machining allows the machine to rotate the part, enabling it to be machined on multiple sides without manual repositioning. This system adds enhanced speed and versatility to machining processes.
Applications:
- Multi-sided machining
- Spiral milling and curved surfaces
- Parts that require machining around a central axis
Industries:
- Aerospace: Airfoil sections
- Automotive: Engine blocks, transmission parts
- Rail: Wheelset hubs
Tolerances:
- ±0.0005″ to ±0.002″
Advantages:
- Increased speed and efficiency
- Reduces human error by automating the rotation of parts
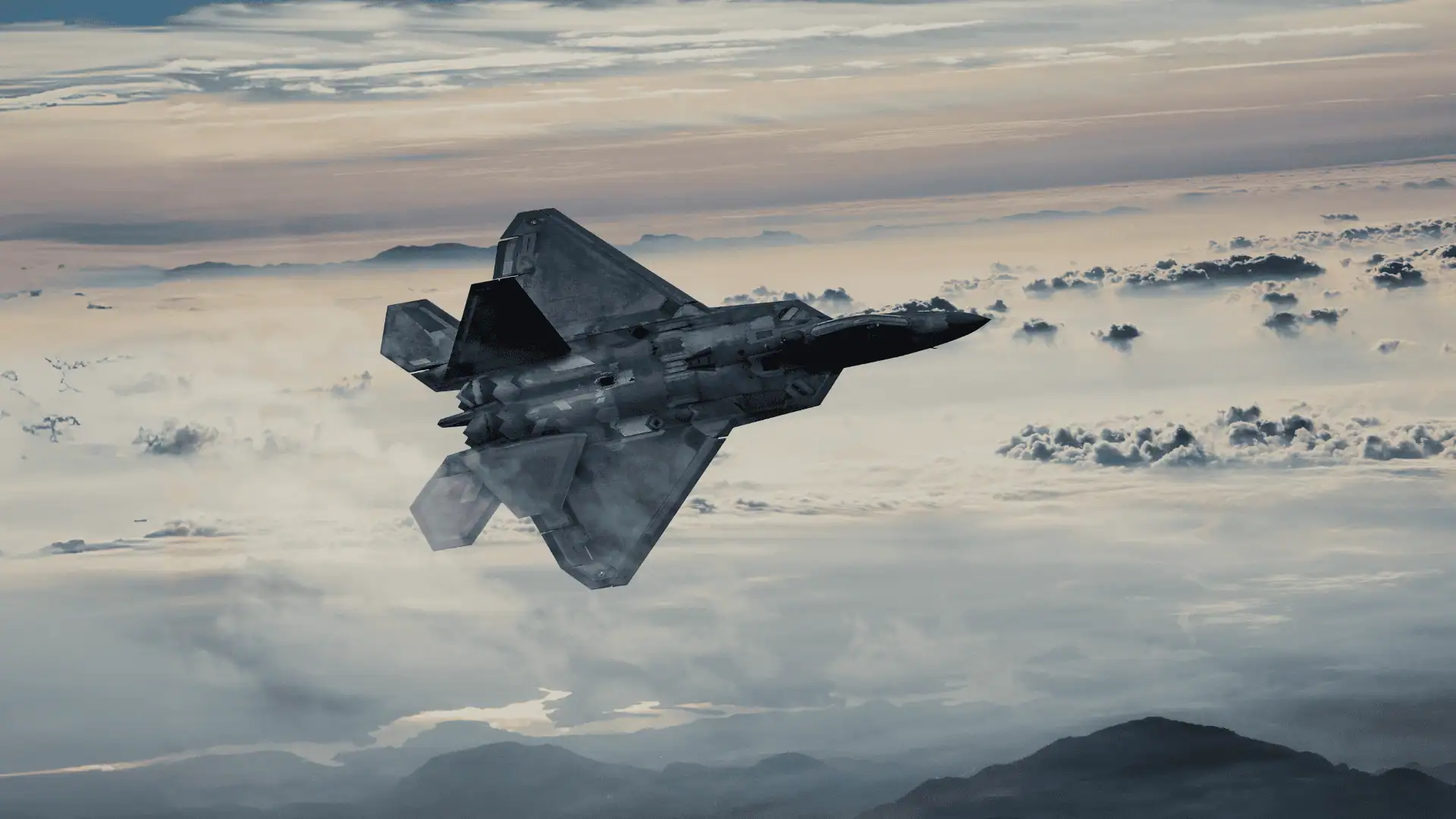
5-Axis CNC Machines
Adding tilting to the rotational axis, 5-axis CNC machines provide even more flexibility, allowing the cutting tool to move along multiple axes simultaneously. This results in higher precision and the ability to handle complex geometries in a single setup.
Applications:
- High-precision aerospace components
- Complex automotive molds and valves
- Rail braking systems requiring angled drilling
Industries:
- Aerospace: Turbine blades, structural components
- Automotive: Fuel injection systems
- Rail: Braking discs, connection systems
Tolerances:
- As tight as ±0.0001″
Advantages:
- Single-setup machining eliminates the need for repositioning, which reduces errors.
- Capable of machining all sides of a part, improving efficiency.
6-Axis CNC Machines
6-axis CNC machines incorporate an additional axis, allowing for more dynamic tool movement. These machines are ideal for producing intricate designs and enhancing speed and cycle times.
Industries:
- Aerospace: Complex geometries for turbine parts
- Automotive: Prototype and EV components
- Rail: Safety-critical assemblies
Applications:
- Aerospace turbine rotors
- Engine mounts and structural parts
- Rail couplers and dampers
Advantages:
- Greater efficiency in manufacturing.
- Capable of complex multi-angle machining in a single run.
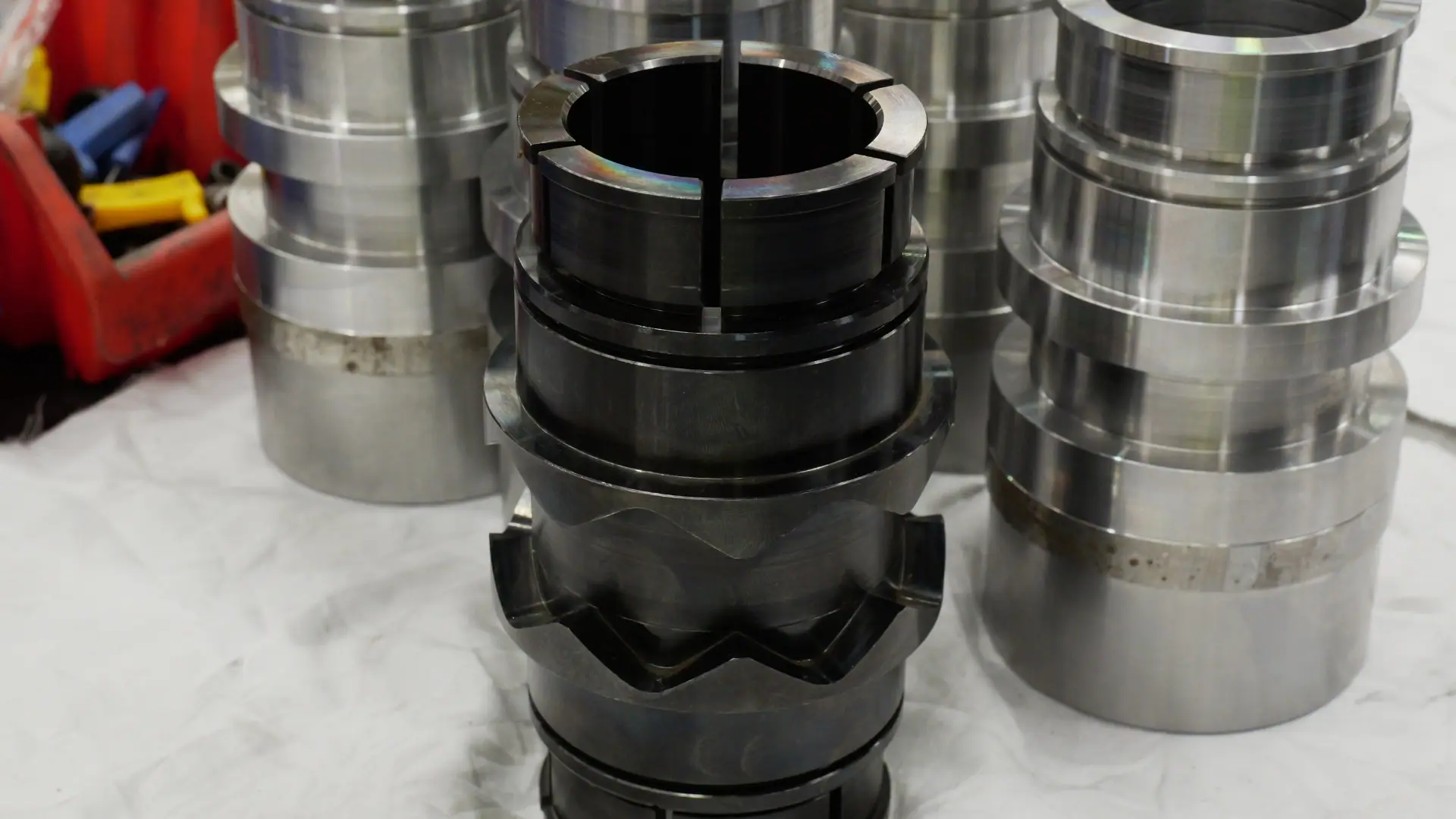
7-Axis CNC Machines
7-axis CNC machines offer the ultimate flexibility in machining, allowing parts to be rotated, tilted, and translated in nearly all possible directions. These systems are ideal for producing ultra-complex geometries and are often used in robotic CNC arms.
Applications:
- Aerospace nozzle assemblies
- High-end automotive parts (e.g., F1 components)
- Medical implants (e.g., orthopaedic parts)
Industries:
- Aerospace: Missile guidance components
- Medical: Orthopaedic implants
- Automotive: Advanced high-performance components for sports and electric vehicles
Advantages:
- Unmatched flexibility and precision
- Extreme accuracy and repeatability, ideal for complex, low-volume production
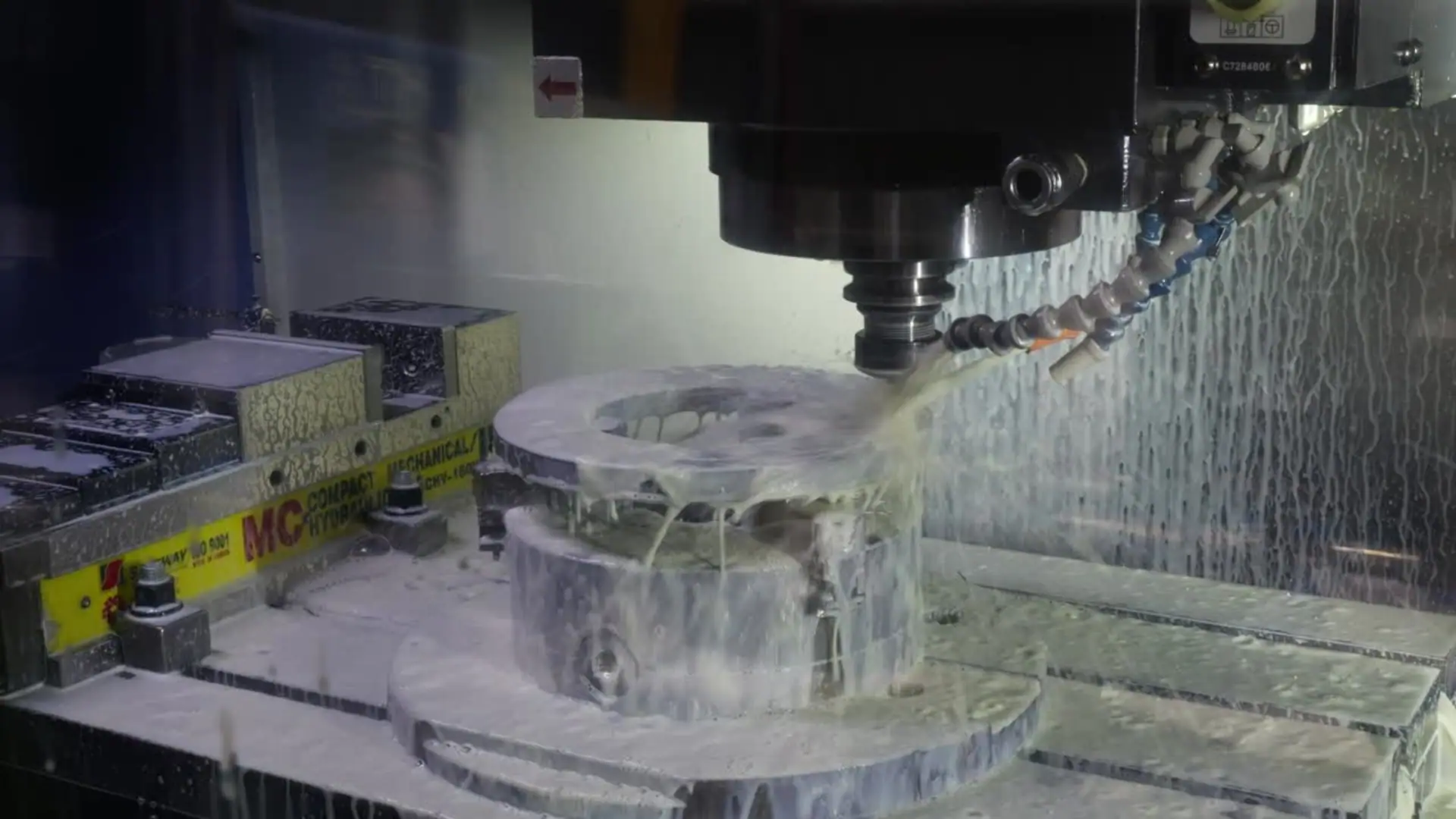
CNC Machines Based on Control Systems
Different CNC machines use various control systems to guide their movements. These systems are critical to the type of operations they can perform and are tailored to meet specific needs in manufacturing.
Point-to-Point Positioning Control
- Ideal for applications where tools need to move from one point to another without considering the path in between.
- Commonly used in drilling and hole punching.
Straight Cut Positioning Control
- Used in processes that require straight-line movements, such as laser cutting or plasma cutting.
- Perfect for sheet metal fabrication where precise straight cuts are needed.
Contouring Path CNC Control
- Enables continuous movement along complex paths, making it ideal for mold-making and 3D surface creation.
- Widely used in aerospace machining for intricate component designs.
Material and Size Considerations
CNC machines are capable of handling a wide range of materials, from soft polymers to hard metals and composites, making them versatile for various industries.
Commonly Machined Materials
- Metals: Aluminum, titanium, stainless steel, Inconel
- Polymers: PEEK, Nylon, Delrin
- Composites: CFRP (Carbon Fiber Reinforced Polymer), GFRP (Glass Fiber Reinforced Polymer)
- Others: Brass, copper, bronze
Part Size and Diameter Ranges
- Lathes: Capable of machining parts with diameters from 5 mm to 500 mm.
- Milling Machines: Can handle parts up to 1000 mm in length.
- High-Axis Machines: Suitable for parts with highly irregular geometries, extending up to 2 meters or more.
How Different Industries Use CNC Machines
Aerospace
- Demands parts with tight tolerances and lightweight materials.
- 5-, 6-, and 7-axis machines dominate for machining high-complexity components such as turbine parts, airframes, and hydraulic systems.
Automotive
- Requires the mass production of reliable, identical components.
- Uses 2–5 axis machines for parts like engine blocks, brake systems, and suspension components.
- High repeatability and speed are necessary for cost-effective production.
Rail
- Focuses on producing medium to large components like wheel assemblies and suspension systems.
- 3–5 axis machines are commonly used for producing components with durability and cost-efficiency in mind.
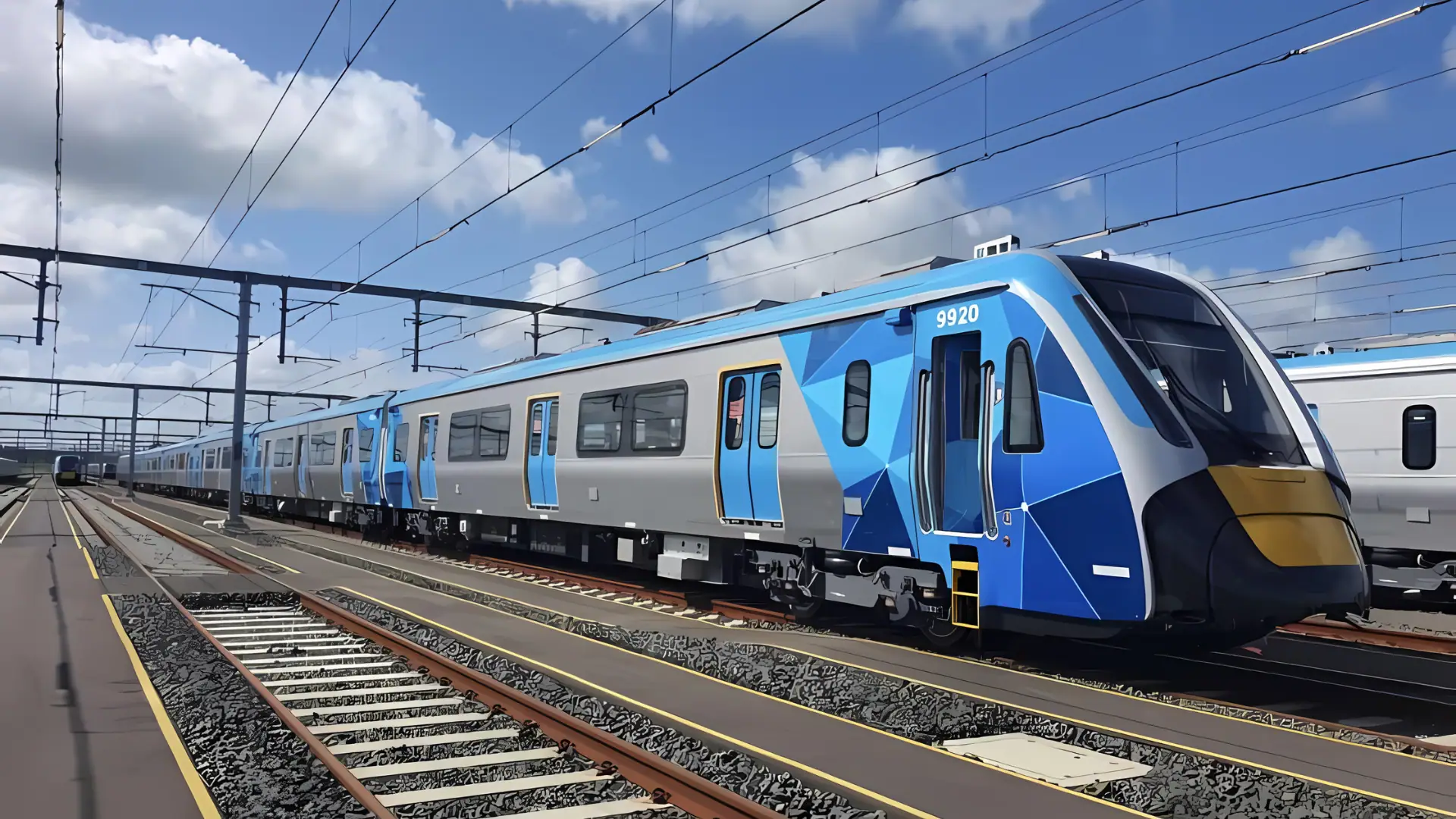
Choosing the Right CNC Machine
Factors to Consider:
- Part complexity: More axes = greater capability.
- Material hardness: Tough materials like titanium require rigid machines.
- Production volume: Choose based on batch production vs. continuous production.
- Budget: Higher-axis machines require a larger initial investment.
- Operator skill: Machines with 5+ axes demand highly skilled machinists.
Final Notes
From basic 2-axis lathes to advanced 7-axis systems, each machine type plays a specific role in meeting the diverse requirements of aerospace, automotive, and rail applications.
CNC machining enables ultra-tight tolerances and complex geometries essential for flight-critical components. In the automotive sector, it supports high-speed mass production with consistent quality. For the rail industry, CNC technology ensures durability and dimensional accuracy for heavy-duty components under extreme conditions.
As manufacturing continues to evolve, CNC technology remains at the core of innovation, helping engineers and machinists push the boundaries of what’s possible with speed, scale, and precision.
Get insights on industry news and posts.
Related Posts
July 24, 2025
Tooling, Fixtures & Jigs Overview | Rail Applications
Tooling, jigs & fixtures is the physical interface between the design and the…
April 22, 2025
What is Precision Machining? Aerospace-Grade Accuracy
Precision machining is the process of removing material from a workpiece with…
November 29, 2024
CNC Machine Maintenance | Expert Guide
CNC machine maintenance is required for proper care to continue performing at…