Types of Welding
Welding is a foundational process in modern manufacturing, fabrication and construction with many types of welding. It plays a critical role in joining metals through heat, pressure and a combination of both.
Choosing the right welding technique is essential for achieving structural integrity, cost efficiency and project longevity.
This overview goes through the most common types of welding used across industries today. Each type has unique benefits, applications and requirements.
Spot Welding
Spot welding is a resistance welding technique that joins two or more metal sheets together by applying pressure and heat generated from an electric current.
This method is widely used in automotive manufacturing, aerospace components, and metal furniture fabrication due to its speed and repeatability.
Key Benefits of Spot Welding
- High speed production
- Excellent for thin sheet metal
- Minimal filler material required
- Clean and precise joints
Despite its advantages, spot welding is typically limited to thin materials and requires access to both sides of the workpiece.
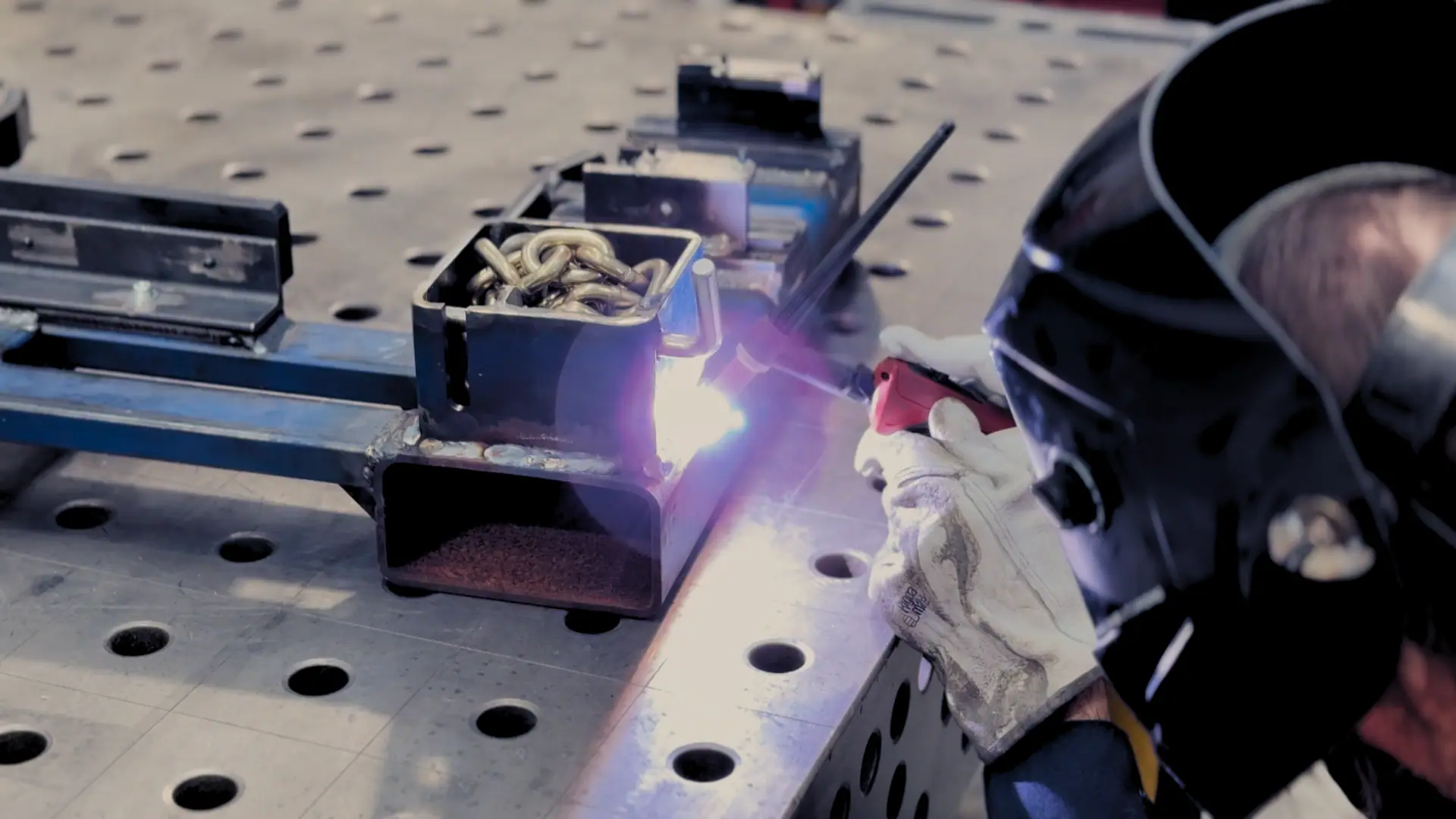
MIG Welding (Metal Inert Gas)
MIG welding, formally known as Gas Metal Arc Welding (GMAW), uses a consumable wire electrode that is continuously fed through a welding gun.
The process is shielded by an inert or semi-inert gas to protect the weld pool.
Why Choose MIG Welding?
- Fast and efficient
- Easier to learn than TIG
- Suitable for thicker materials and long weld runs
- Widely used in industrial fabrication and home DIY
MIG welding may not produce welds as precise as TIG, and it is less effective outdoors due to sensitivity to wind affecting the shielding gas.
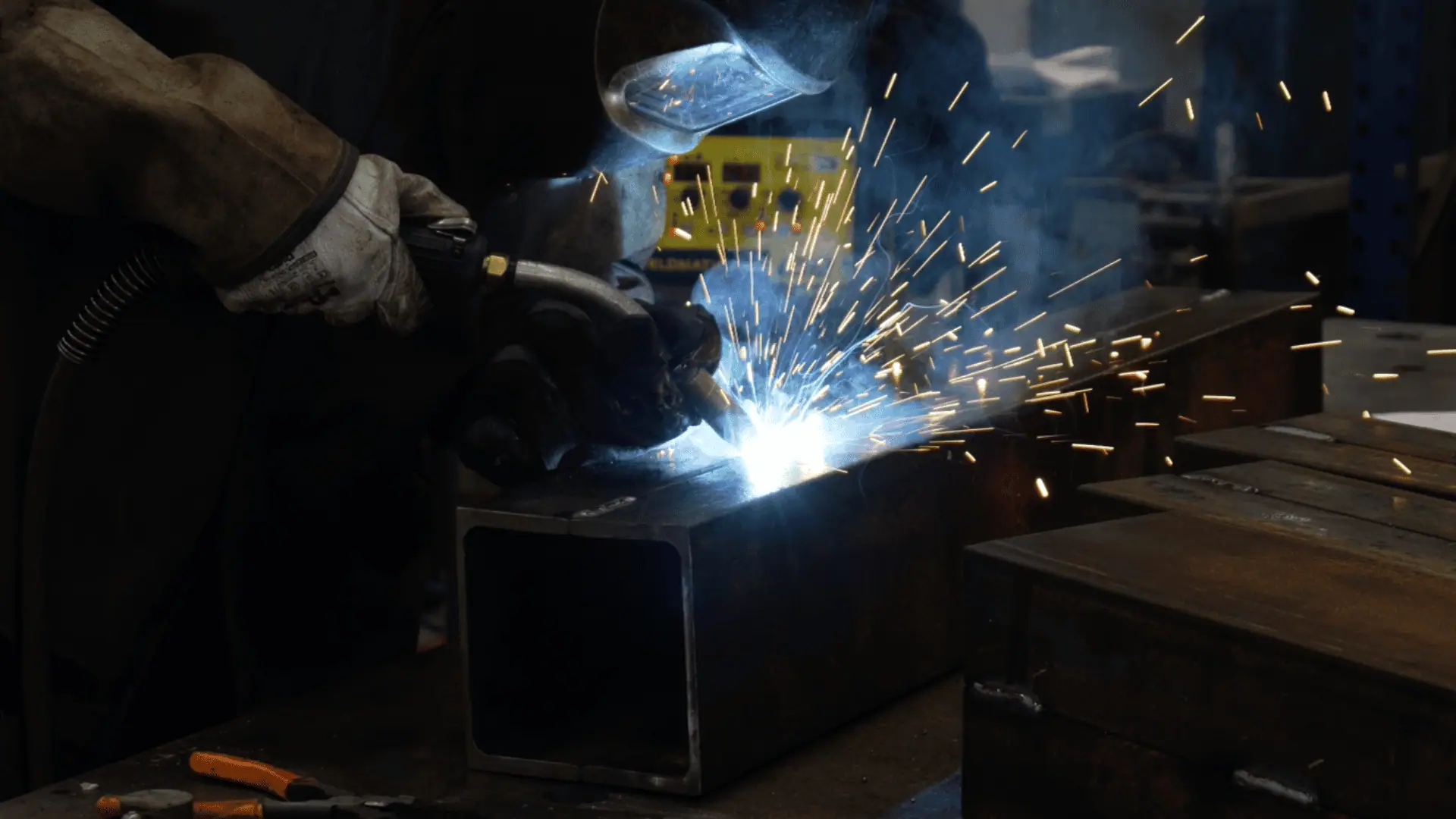
Fusion Welding
Fusion welding is a broad category that includes all welding methods where heat is used to melt the base materials.
Unlike solid state welding, fusion welding involves the melting and fusing of metal at the joint, often using filler material.
Core Characteristics of Fusion Welding
- Applicable to various base metals
- Allows deep penetration and strong joints
- Supports automated welding systems
- Includes subtypes such as arc, laser, and electron beam welding
Fusion welding is highly versatile but often requires strict control over temperature and technique to avoid warping or defects.
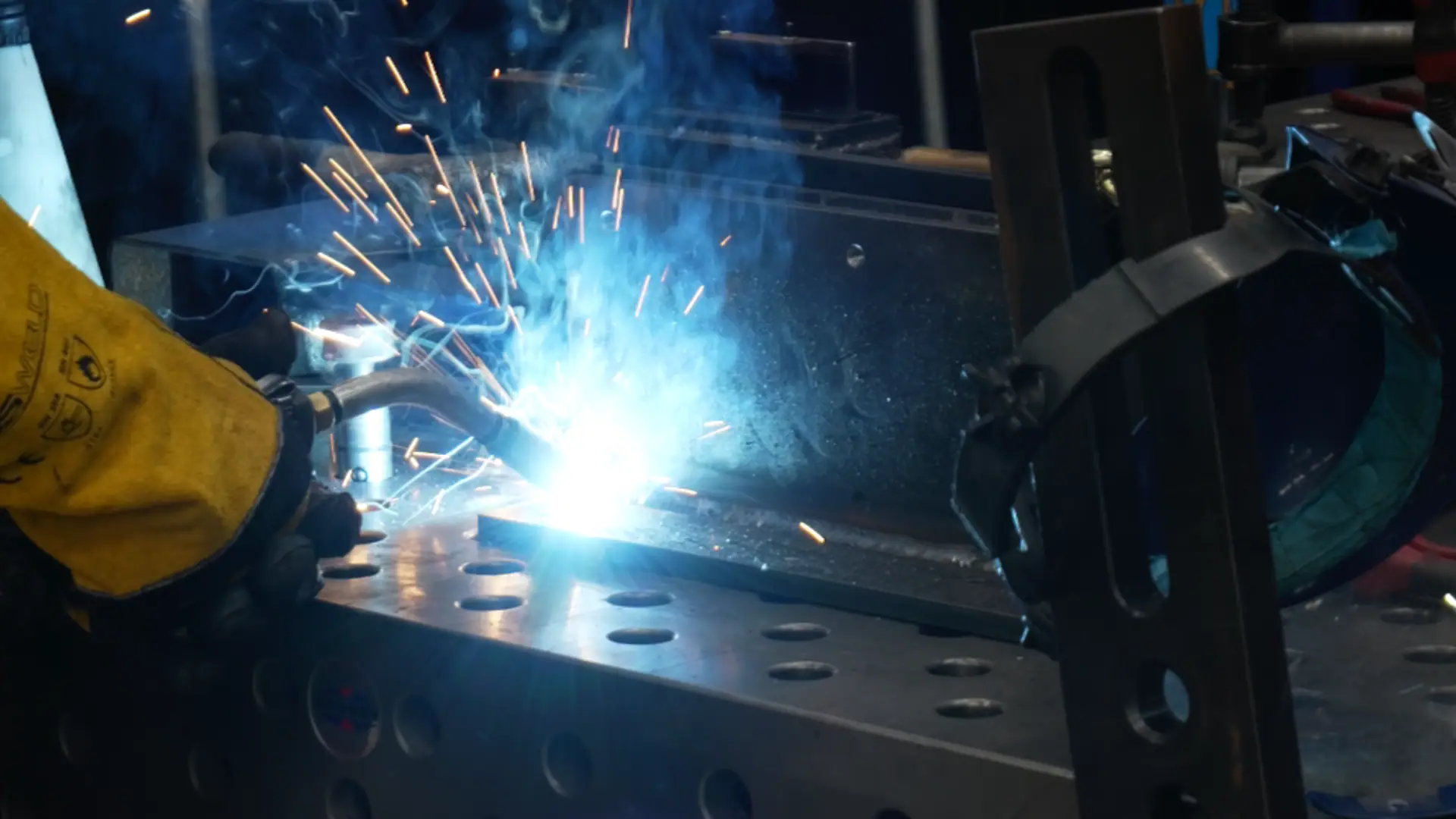
Final Notes
Welding is not a one size fits all process. Each method, whether it is spot, TIG, MIG, or fusion, serves a specific purpose depending on material type, thickness, precision requirements, and production speed.
Understanding these core welding types will help engineers, fabricators, and project managers select the most appropriate method for their applications.
Get insights on industry news and posts.
Related Posts
February 25, 2025
What is Fusion Welding | Types and Processes
Fusion welding, also known simply as metal welding, is a process where two or…
October 1, 2024
How to MIG Weld
MIG welding is one of the most versatile and user-friendly welding processes,…
September 24, 2024
What is TIG Welding? | Comprehensive Overview
TIG welding is a fusion welding process that uses a non-consumable tungsten…